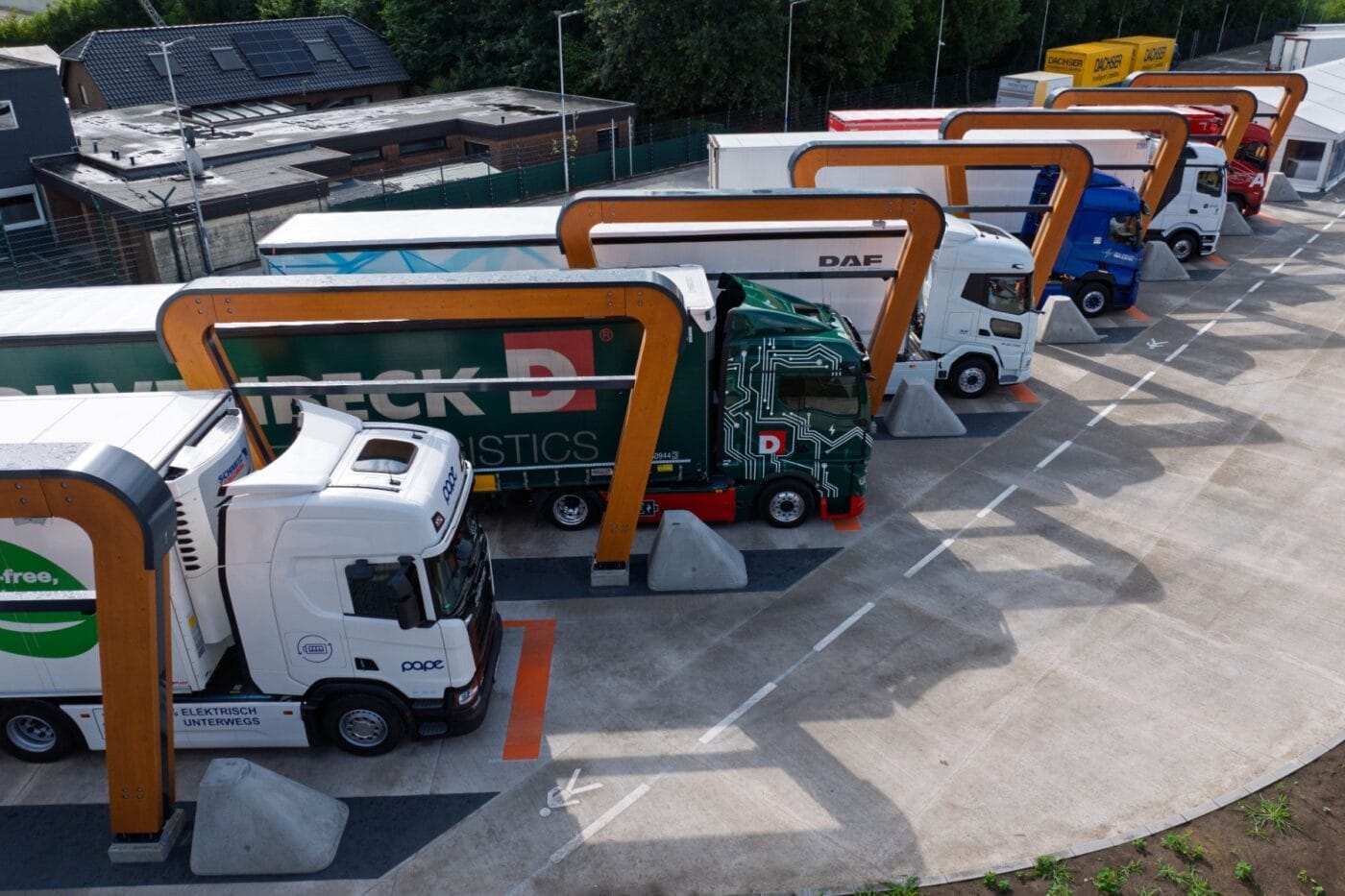
“The technology is ready – now it’s about cost and scaling”- Interview with Anders Grauers on the future of electric trucks
Chalmers University of Technology, located in Gothenburg, is one of Sweden’s foremost technical universities, renowned for its close collaboration with industry and strong emphasis on applied research to tackle real-world engineering challenges. The university’s work spans energy systems, sustainable transport, materials technology, and digitalisation, with a clear mission to accelerate the transition to a fossil-free society.
Grauers has spent much of his academic and professional career focusing on electric vehicles, electric road systems, battery dimensioning, and energy efficiency strategies for commercial fleets. His research is deeply rooted in practical application, often conducted in collaboration with major industry players in Sweden and across Europe. Grauers is particularly known for his systems-level analysis of electric transport solutions, weighing not only technical feasibility but also operational, economic, and societal dimensions.
In this conversation with electrive, he shares his perspective on the development of battery-electric trucks, the role of hydrogen, and the real bottlenecks in the current transformation of road freight. Contrary to the common narrative of persistent technological hurdles, Grauers argues that most fundamental technical problems for battery-electric trucks have already been solved. He sees the remaining challenges as primarily economic and organisational rather than rooted in engineering impossibility.
We spoke to him on the bustling exhibition floor at EVS38, where the optimism around electrification was palpable – but so was the realism about grid integration, infrastructure rollout, and cost competitiveness. Against this backdrop, Grauers’ insights provide a refreshing, pragmatic assessment of where we stand today, what needs to happen next, and why the electrification of trucks might proceed faster – and more smoothly – than many still assume.
What do you see as the biggest technical hurdles for electrifying the trucking industry?
The answer is: there are actually, no technical hurdles.
No technical hurdles?
We’re not waiting for any new technology. The main challenge is cost – and that’s not really a technical hurdle. It’s about volume. Costs come down as volumes increase. That’s one of my frustrations: people often don’t realise how well things are going, and how many of the fundamental problems we’ve already solved.
If we look back 20 years, everyone agreed there was no solution for heavy trucks. None whatsoever. Everything was either impossible or too expensive. Today, I’d say we have two or three solutions for long-haul trucks: battery-electric trucks with stationary charging, hydrogen trucks, and maybe electric road systems. All of them will work if needed. It’s just a question of which is best.
How will people notice these hurdles are gone?
One issue is that we want this transition to happen very quickly. Normally, transitions aren’t quick – and a rapid transition can be painful. We need some patience, but there’s still a lot we can do to speed it up: informing people, demonstrating what’s possible. I’ve been involved in big projects with hauliers, OEMs and charge point operators. They show this is doable and act as good examples. But we also need more focused policy to accelerate the transition. Policy and spreading knowledge are equally important.
You also mentioned cost. How does your research address the trade-off between battery sizes, cost, and vehicle range for electric transport?
For commercial vehicles, it’s not the same as cars. Batteries aren’t a cost problem – they’re a weight problem. If it were only about cost, even today’s battery prices are low enough to buy a battery that covers a full day’s drive with a decent margin. It’s weight that prevents us from simply upsizing.
For many trucks, weight isn’t an issue because they only need to drive, say, 300 kilometres per day. Then you just buy a battery for a full day’s operation. There’s also a misunderstanding about battery costs: minimising battery cost doesn’t necessarily mean minimising battery size. A smaller battery has a shorter lifespan. In principle, upsizing slightly saves money because it lasts longer. The extra 20–25% margin is almost free – if you don’t have a weight issue.
It is all part of the TCO, the total cost of ownership.
Exactly. The bigger challenge is smart charging strategies that don’t reduce productivity. For most hauliers, it’ll be simple: they’ll have the charging they need for daily operations, plus some supplementary public charging if plans change. For long-haul trucks, it’s more complex because they’ll need to charge 40–50% of their energy daily on public chargers – and that needs to be cheap.
Our studies show it will become cheap enough, but it has to be about half today’s price before operators invest in long-haul trucks. Charge point operators, however, struggle to make money at those low prices during the transition. Eventually, it won’t be a problem, but building out new charging infrastructure is financially difficult in the first year.
Public fast charging for cars or supplementary charging for trucks is easier to start with, because you can charge a higher price and it’s still worth it. We’re seeing quite a successful transition on the car side. Even if public charging should become cheaper, it’s already cheap enough.
So the cost of public charging for long-haul trucks needs to come down by half?
Yes, to about 25 euro cents per kilowatt hour. Otherwise, hydrogen becomes a cost-effective alternative. If charging is too expensive, we’ll go the hydrogen route. If it’s cheaper than that, we probably don’t need hydrogen.
Do your studies indicate how long it will take to reach that price level?
That’s the problem – I can’t say when. It depends entirely on utilisation of chargers. Once energy utilisation reaches around 20%, we’ll meet that target. Competition will also push down prices. The charging market will be very competitive.
Let’s talk hydrogen fuel trucks. What role will they play in the fleet mix in Europe?
My guess is they’ll be a niche solution. I’ve studied battery-electric trucks in detail and hydrogen trucks only as a comparison. Current hydrogen cost estimates are roughly on par with diesel trucks, which is good – but I think battery-electric will beat that. Hydrogen may suit segments where even fast charging isn’t fast enough, or where you carry such heavy goods that every tonne counts. So there will be niches, but I don’t think hydrogen will be the main solution. Even for long haul, I think battery-electric will dominate.
Why are OEMs still investing in hydrogen long-haul trucks?
Because it’s a close call. If hydrogen is slightly cheaper, it wins. It’s a tipping point, very sensitive to cost assumptions. Also, many people still don’t realise how many problems around battery-electric trucks have been solved. There are misconceptions about megawatt chargers being prohibitively expensive. Per unit, yes, but per kilowatt hour delivered, they’re not more expensive than other fast chargers.
Yet, if you ask a utility to build a site with 50 megawatts of chargers, they’ll look frightened because it’s new to them. But fundamentally, there’s no problem building such sites. Electric grids are cheaper the bigger you make them. It’s easier to build one 50-megawatt site than fifty 1-megawatt sites.
What about all the arguments that the grid can’t handle it?
That’s like saying you can’t build new houses because there are no roads. Of course you build the roads. It’s infrastructure. The cost will be paid for. The only real problem is timing – it takes time to build. There’s also confusion because grids are getting more expensive per kilowatt hour, but that’s due to reinvesting in old systems without new income.
When you build new charging infrastructure, you create a new income stream to pay for the grid expansion. So yes, building more is necessary. Smart charging can reduce costs by 10–20%, but it won’t eliminate the need to build.
Sometimes people say, “This costs 100 million euros,” and stop there, assuming it’s too expensive. But if the transport system you’re serving is worth 2-3 billion euros per year, that’s a small cost. Same with batteries: paying a little extra often saves money overall. It’s about perspective.
You mentioned policy earlier. Is that key to speeding things up?
Even without new policy, it will happen eventually. But if we want it faster, upfront subsidies for trucks are one of the most effective tools. I don’t think we should subsidise charging or grids too much – those costs are about right and encourage efficient use. Subsidising trucks, though, puts them on the road, creating demand for charging, which then justifies building the infrastructure.
Should subsidies be national or EU-level?
EU-level is good. But I’m frustrated that, for example, Sweden recently removed diesel price increases linked to biofuel mandates. Higher diesel prices support electrification. I want to see market-driven transitions. Once the market starts moving, it gains momentum. We just need to push the right buttons.
Did Norway get it right?
We should be grateful to Norway. They showed it’s doable and that the problem isn’t users – it’s cost. Once cost came down, adoption took off. But there’s no need to repeat exactly what they did.
Looking ten years ahead, what technological developments in electric transport will surprise people?
I don’t expect extreme changes. We don’t need them – just steady improvements. In ten years, people will look back and wonder what the problem was. For electric cars, charging concerns become irrelevant once you build a routine around them.
For companies, the transition will be painful, but the end result is positive and profitable. Hauliers are professional. Charging will just become another part of their already complex planning. They’ll integrate it well, but we should support them and showcase good examples.
Thank you, Mr. Grauers, for speaking to us. That might just be the most positive outlook I’ve heard today.
2 Comments