Direct eDrive: Universal drive for small series
Jens Broedersdorff and Uwe Koenzen were looking for a powerful but compact electric motor for a sports car project. Because the drives available were too expensive, they developed an electric machine, which they found curiously applicable.
It all started with a sports car. Some investors want to finance an independent sports car project – with electric drive, of course. They turn to their friends Jens Broedersdorff and Uwe Koenzen. Under the name “Classic eCars”, the two not only develop and design retrofit electric drives for vintage cars from the Beetle to the Jaguar E-Type, but also advise companies on the transition to e-mobility – they have, among other things, contributed to the charging park and the logistics of the electric delivery vans at the bakery Ihr Bäcker Schüren, which is well-known in the eMobility world.
Broedersdorff and Koenzen are looking for a suitable motor. But after a few conversations with “the usual suspects”, they realise that the available engines with the right performance data are scarce. “We asked well-known manufacturers of electric motors, but because of the special requirements, the offers were all costly and only available in minimal quantities,” says Broedersdorff. “We, therefore, decided to develop an electric motor ourselves for this application together with Engiro.
Founding & Development
Engiro was founded in Aachen in 2010 and, according to the company’s homepage, specialises in the development and production of “high-performance electric machines, electric gearboxes and drive systems”. The company is closely linked to the RWTH through its management and scientific advisory board.
It quickly became clear that the engine should be as efficient as possible. In contrast to a large SUV, a sports car has less space for batteries – and if both sporty driving performance and an appropriate range are to be possible, the engine must use the available power sparingly. This is one of the reasons why the project partners did not use an otherwise customary gear ratio in the design. Instead, the power is transmitted directly to the drive shaft via a specially developed hollow shaft – hence the project name “Direct eDrive”.
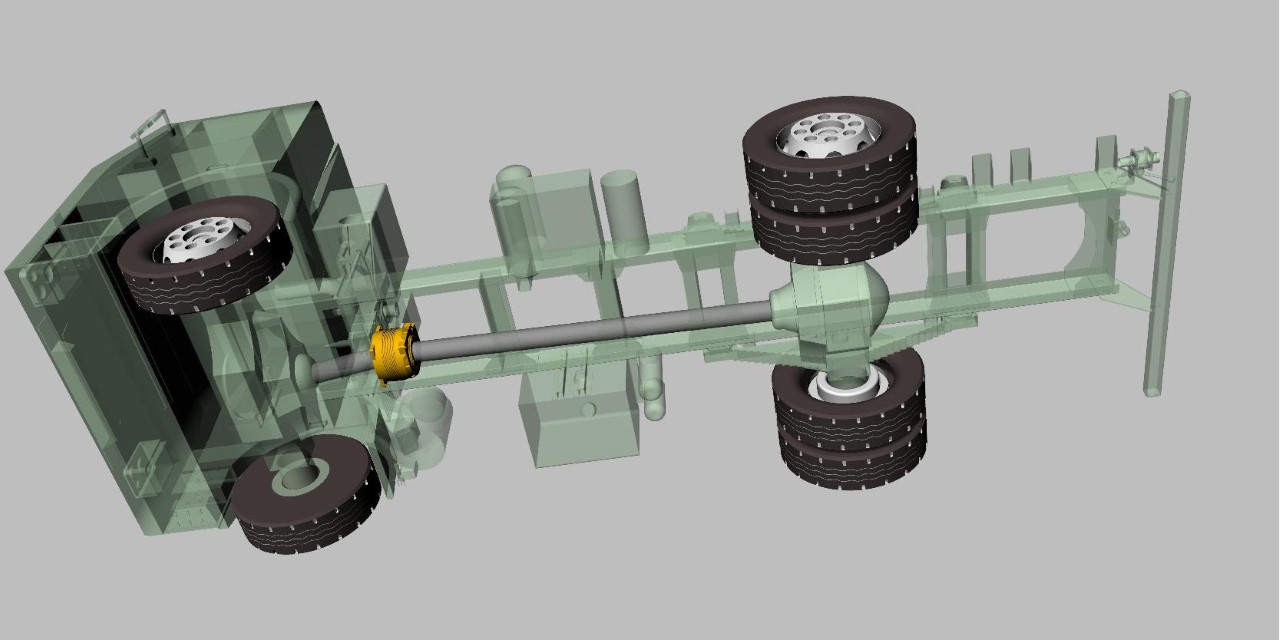
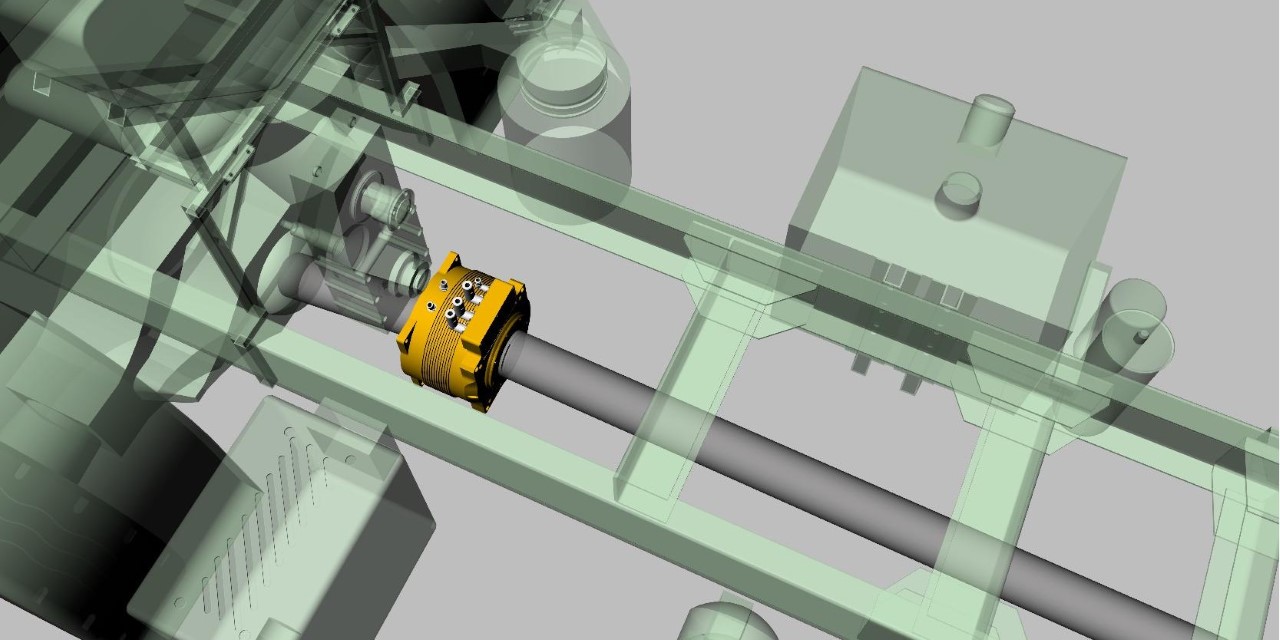
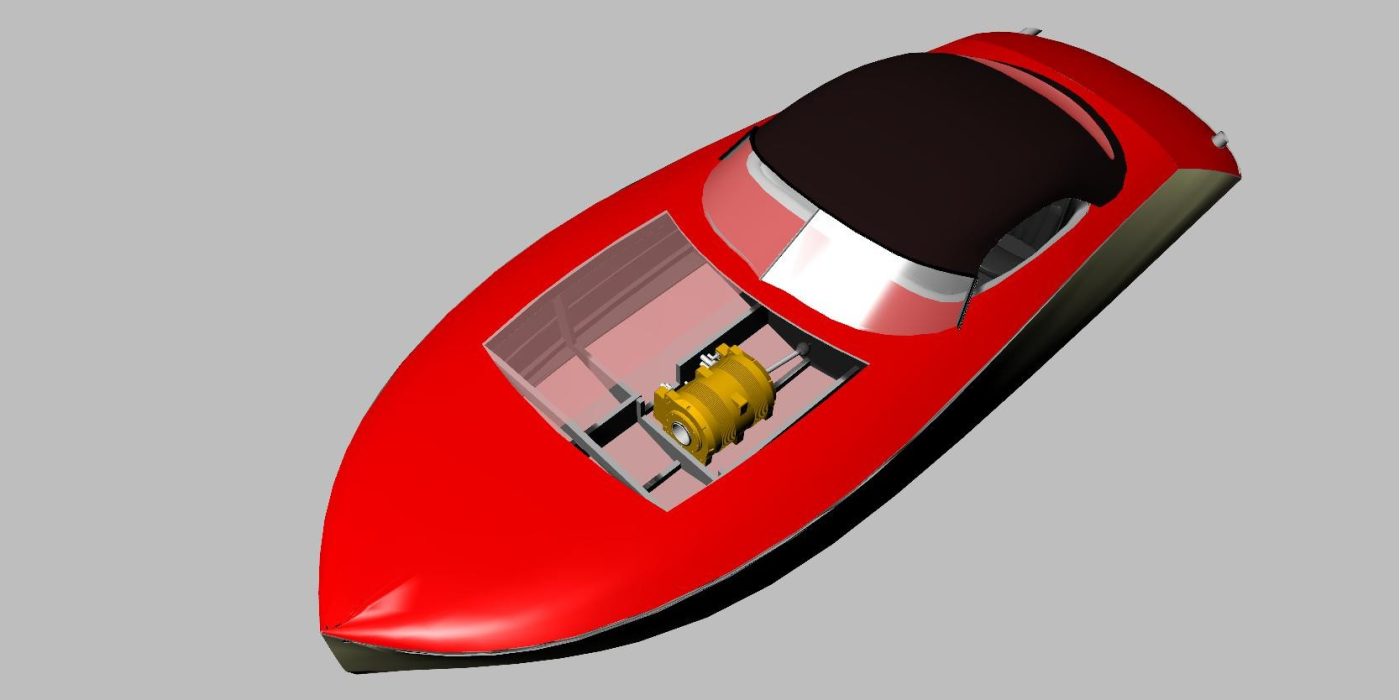
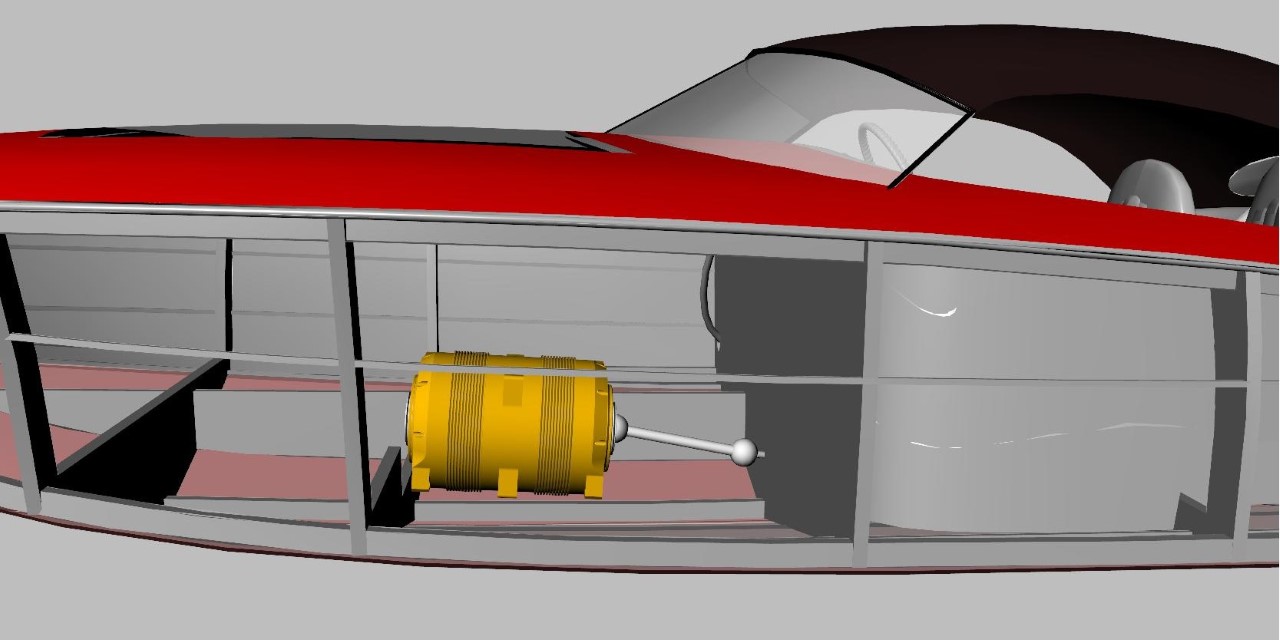
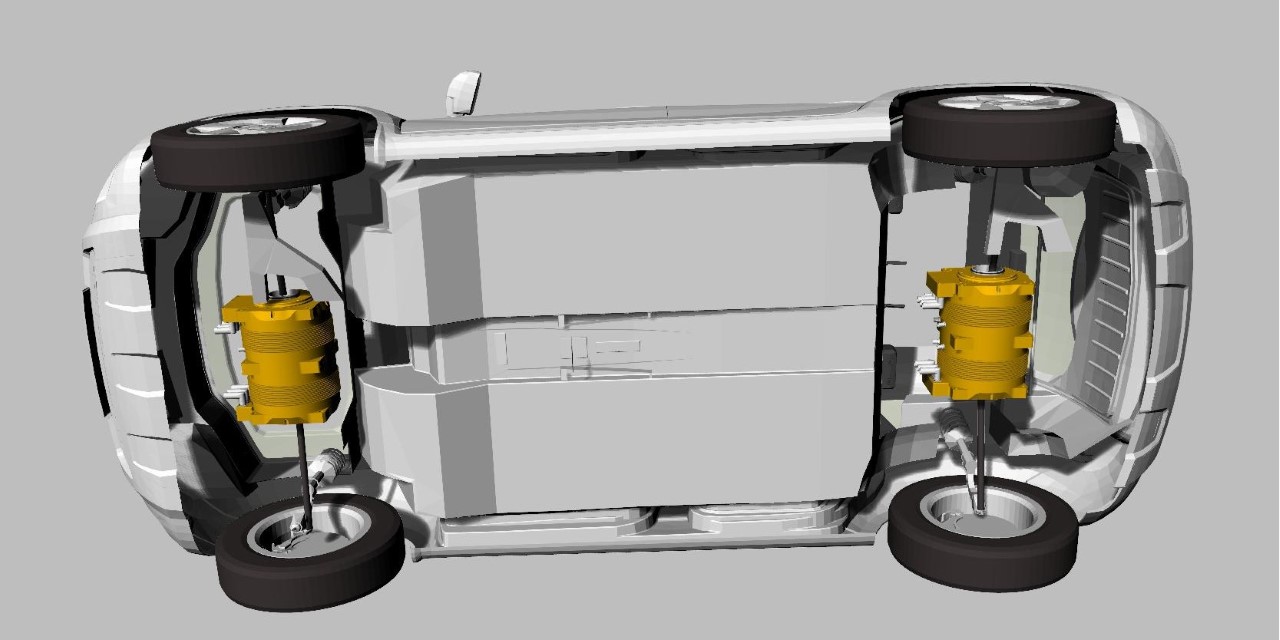
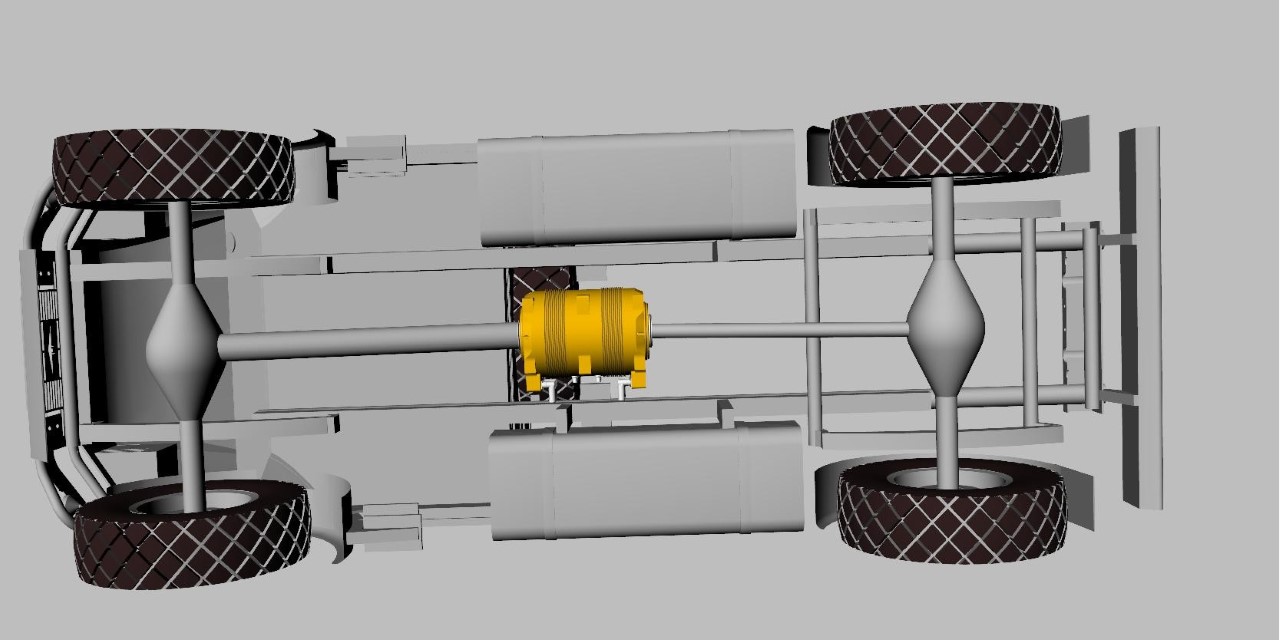
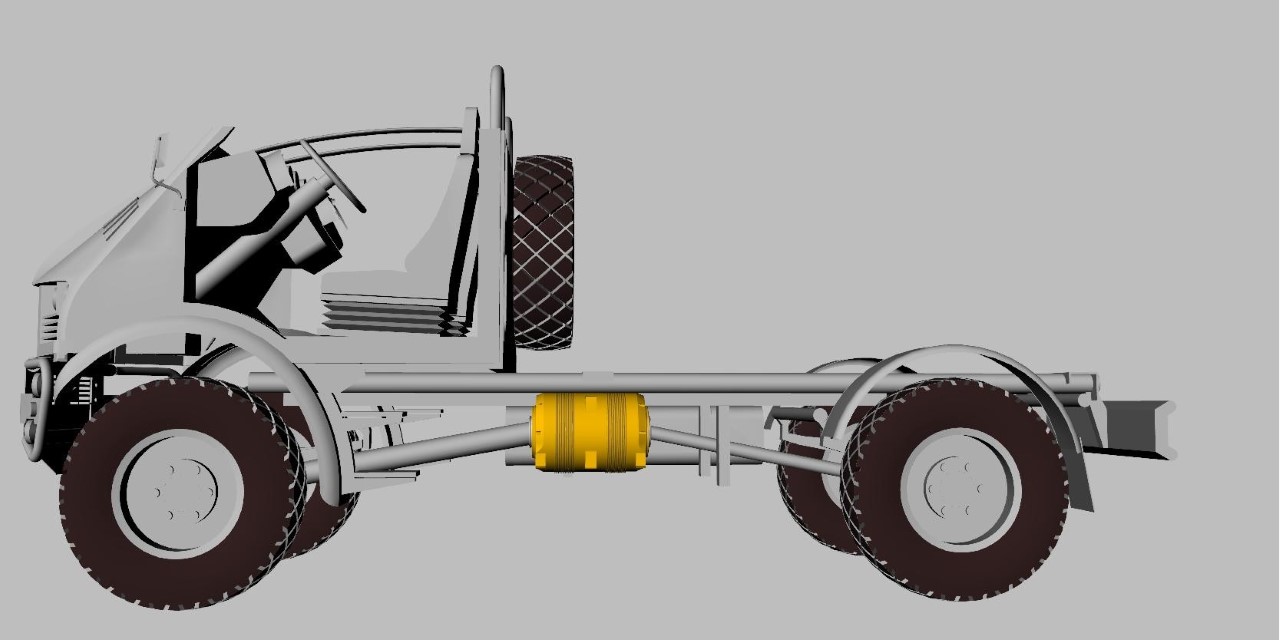
“The simulations not only showed that our concept works, but the specifications can also even be exceeded in many respects,” says Broedersdorff. “There is no comparable solution on the market,” adds Koenzen. “These are all solutions with transmission and high-speed concept.
Double application
Another special feature of the design: It can also be used as a twin motor. This results in numerous options for the use of permanently excited synchronous motors. With one motor per axle, one mechanical differential is still required. If, however, two motors are mounted “back-to-back” on one axle, the mechanical differential is also eliminated – the differences between the two sides of the vehicle are then compensated by software. Or if two engines are mounted on the cardan shaft in a 4×4 commercial vehicle, they virtually replace the centre differential. We have summarised some of the simulated applications from the truck hybrid with one engine to the high-performance passenger car with two twin engines in the gallery.
With different motor arrangements, different power ranges can also be covered. An electric motor delivers 100 kW continuous power and 259 kW at peak over ten seconds – so 518 kW per axle and up to 1,036 kW in the vehicle are possible. In the configuration with two twin motors, targeted distribution of the torque per wheel is also possible, as its motor drives each wheel. This torque vectoring enables better traction – whether in a sports car or an off-road vehicle on slippery surfaces.
“Although the engines were developed for a sports car, they can be used thanks to the speed range and the twin-engine design very flexibly, since the wheel sizes in passenger cars, for example, hardly differ and the cardan shafts can be driven in truck applications,” says Koenzen. A sedan or SUV is, therefore, also conceivable. In commercial vehicles, the wheels are much larger, but unlike sports cars, the maximum speed is irrelevant. According to the two developers, it should even be possible to use them in boats.
Efficiency
Despite the performance data and variability, the efficiency should be over 96 per cent. “We have a very high efficiency not only because of the missing transmission. Engiro worked on the electrical design for a very long time and simulated well over 100 designs,” says Broedersdorff. “With the result that we not only have a high peak value in a small range, but the engine also works very efficiently over a wide speed range.
The efficiency is not only simulated but measured. “These engines don’t just exist as renderings, they are fully functional prototypes and have been put to the test,” says Koenzen. The two developers were so satisfied with the values that they are now looking for additional partners to produce a small series. The drive is unsuitable for mass production, and the performance data mean that the use of materials such as neodymium and copper is high.
Retrofitting
Not only the sports cars mentioned are possible, but also retrofit solutions for trucks or special vehicles from Unimog or Bremach. According to Broedersdorff, special vehicles in mines or mining, as well as boats, can also be equipped with the machines. Depending on requirements, the machines can be supplied with or without power electronics. On request, the developers can also help with the implementation of the drive.
0 Comments