Interview Frank Mühlon: ABB executive sees demand for cheaper charging solutions
With over 14,000 DC charging stations installed, the Swiss ABB group is among the biggest suppliers of charging infrastructure. The market is developing quickly and will continue to change at a rapid pace in the coming years.
In this interview, Frank Mühlon, Head of ABB’s Global E-Mobility Infrastructure Solutions, talks about new products in the AC, DC and HPC sectors, and changing needs of the B2B and consumer trade.
***
Mr Mühlon, ABB has been offering AC wall boxes for some time now. How satisfied are you with this development?
The AC segment is an entirely different affair to the well-known DC segment, and we were aware of that. We also wanted to learn how this segment differed. We have been able to learn some lessons and recently had the market launch of our new Terra AC Wallbox. We designed it to meet the growing demand for charging stations that are both high quality and at the same time, affordable to integrate into homes and business premises. Besides, it targets the growing number of renewable energy users who want to manage their power consumption.
Can you give examples of what the company has learned?
For us, DC charging is a project business done directly with partners. In the AC sector, the number of chargers and the number of customers is significantly higher, so it is challenging to scale direct trade with consumers. Here, sales are also made through intermediaries. However, there are also individual large-scale projects in the AC sector that we handle directly – that’s not mutually exclusive. Sounds simple in theory, but everything must first be established and adapted again and again.
And if you look at quantities?
The quantity was secondary in this project. Nevertheless, it led to ABB’s decision to invest in the AC segment and to continue to grow with it. As a result, we looked around for acquisition and took over ChargeDot in China. The acquisition strengthens our relationship with leading Chinese electric vehicle manufacturers and expands our e-mobility portfolio with hardware and software designed specifically for local requirements.
You stated in October that the takeover should be completed “in the coming months”. Has that come to pass in the meantime?
Yes, we closed the deal a few weeks ago and since have already received two important orders. One involves several thousand wall boxes for a construction project in China, and we are now the charging partner of a Chinese OEM joint venture. At the moment, ChargeDot still focuses clearly on China, but there too, we have to adapt the product range to our requirements.
At the moment? Will that change?
Of course, we are working on developing other products on this technology platform that will meet European and North American requirements. But I cannot give a date.
There are countless AC wall boxes on the European market. How does ABB intend to stand out from the competition?
Differentiation in the AC sector is much more difficult than in the DC sector, that’s true. But we know this at ABB – it is no different from selling surge contactors and circuit breakers for domestic installations, to give just two examples. As an engineer, I can think of a few arguments, but for consumers, other things count like the distribution channel and partner cooperation. That’s precisely our strength, and this is why our wall box will stand out from the rest: a good product at a reasonable price and customers can rely on our large sales and service network.
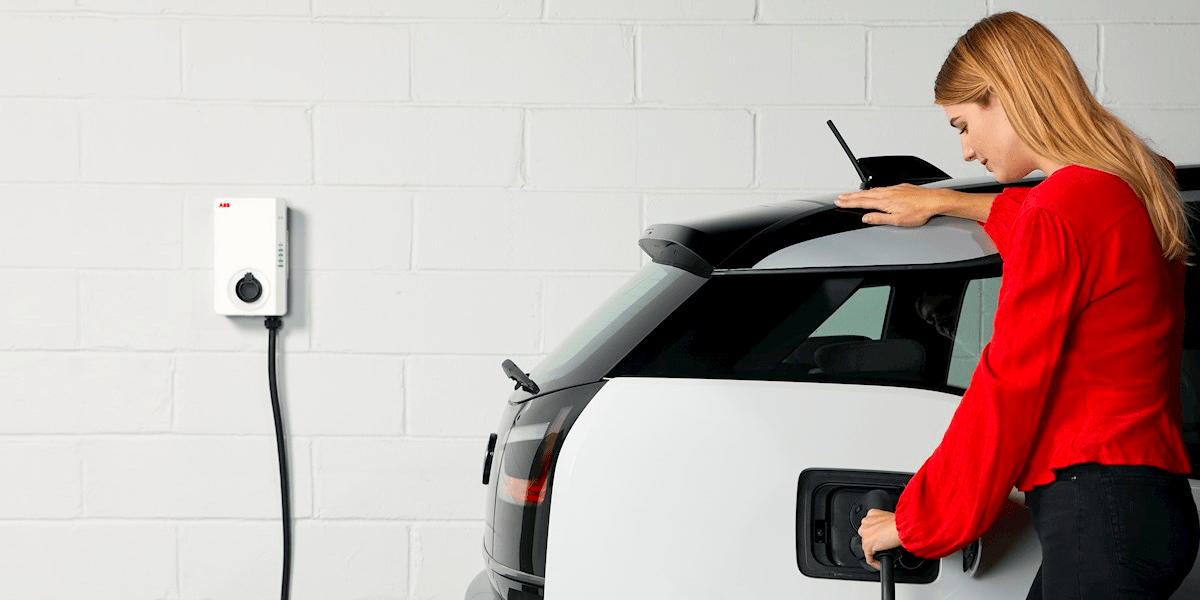
ABB also offers DC wall boxes. What is the demand there? The devices are much more expensive than an AC wall box.
We see quite good and increasing demand in the 20 kW class! With such products, we bypass the AC-DC converters in the vehicle, which are usually designed for a maximum of 11 kW. But with 24 kW charging power, we achieve a reasonable charging speed, while at the same time the requirements for power connection and installation remain manageable. It is still a wall box that can be mounted quite easily, making it much cheaper to install than a DC charging station, which requires a foundation.
Will DC wall boxes become established in the long term and catapult the AC onboard charger out of the electric car?
No manufacturer will go that far at present. If they would, I wouldn’t even be able to charge with an emergency charging cable at a household socket if I were stranded somewhere. But we do see the desire to keep onboard chargers as small as possible. This, of course, limits their power, and that is the determining factor for the speed of AC charging.
Who do you target with the DC Wallbox?
It is a separate application: In car parks, shopping centres and restaurants in city centres, I can recharge more than enough power or even fully charge a car during an average two to three-hour visit. But we are also seeing demand from car dealers who want to hand over fully charged vehicles to their customers after changing or repairing tyres, or after a test drive – all with the advantage of easier installation.
But the private consumer will stay with AC?
For the most part, yes. But we also see demand for even smaller DC wall boxes that are bi-directional. Such devices in the 11-kW power class will then again be attractive for private customers. I’m not just talking about Vehicle2Grid, but also Vehicle2Home, if I have an in-house photovoltaic system and stationary energy storage. Is still a very young market – also due to the lack of appropriate vehicles – but we consider the topic as being very much on the rise. And this field runs better via direct current if I want to connect the two batteries in the car and house.
Where do you see the future of DC charging stations? In recent years there has been much talk about high power charging and 350 kilowatts. But there are still very few vehicles on the market that can even take over 200 kilowatts of charging power.
There was and is a demand for 350-kW chargers from some charging providers and car manufacturers – we have developed our charging station accordingly. There will be more vehicles with 800-volt technology, and the advantages are clear: voltage is cheaper than electricity. At the moment, however, it’s still a matter of economies of scale, there are simply few 800-volt components on the market. I can well imagine that other OEMs will have to follow suit as soon as a volume manufacturer goes to 800 volts and a market develops there.
And once there’s a market for these vehicles, the market for corresponding charging infrastructure will also grow. We still see the trend, yes. But we also know the demand to make cheaper products. How long does it really take for the great mass of vehicles to be able to charge with such services? The market is fanning out somewhat at this point.
Do you want to meet this demand?
We are expanding our range. The question is, how high can I go in charging power without needing a liquid-cooled cable? Then the wires are more expensive and heavier, and above all, I have to integrate a cooling circuit. Besides, the maintenance effort increases with cooling. With this in mind, we will be launching a new charging station that is designed for a maximum of 180 kW and does not require liquid-cooled cables.
The current generation in the 150 to 175 kW class already has liquid-cooled cables. So how can a 180 kW column manage without them?
It’s all about electricity again. A 175 kW column with liquid-cooled cables can handle up to 500 Amps charging current so that I can charge vehicles with 150 kW or even at 400 V. Without liquid-cooling, the cables become either too hot or too thick, so that the limit here is currently 200 A, with derating. Or you use cables with a larger diameter, even for a short time up to about 300 A. However, the main application of a 180 kW column is the parallel charging of two vehicles with 90 kW each. This is sufficient for most types of cars at the moment, especially in urban environments.
What do I need as a CPO today to be well-positioned in the coming years?
That depends on where the CPO wants to set up the station and their use case. The customer doesn’t want to spend much time on the motorway or other thoroughfares, where high charging performance is crucial for the operator and users. At a location where users stay longer, the situation looks different, and I can instead build more charge points with the same budget. Of course, the CPO does not have to commit to one type.
So the solution is offering charge points with different charging capacities at one location?
Exactly, we see an increasing number of such requests in projects. Several 350 kW columns can be combined with a 100 kW charger or the new 180 kW model.
Is there still a market for 50 kW DC pillars?
Yes, on parking lots with slightly higher retention time. For example, supermarkets, where our products are already in use today. I don’t need 350 kW there, but I park for a much shorter time than at the shopping centre with the DC wall box. This segment is still in demand.
What is the focus of development?
We are currently closing the gaps in the portfolio, where we also see demand. That’s why we are not developing a 1-megawatt charging station, but rather the cheaper 180 kW charger or the bidirectional DC wall box. On the other hand, it is about further developing the technology as such. One example: The liquid-cooled high power chargers came to market at an enormous speed. There is a lot of potential here to use better technology to make products more reliable, more efficient and less expensive.
ABB has been a Formula E sponsor since 2018. Is electric motorsport a development lab for you? Participating manufacturers regularly claim it is for their racing cars.
That’s an exciting discussion. What is technically possible for an engineer’s heart? And what is commercially viable? Formula E is a testbed for us to try things out – for example, in the Jaguar I-Pace Trophy. There we are close to series production, but still freer than in large-scale production. We learn a lot here.
What do you think about the discussion that with the Gen3 cars coming in, Formula E might consider pit stops for recharging?
The requirements for a pit stop in a Formula E race are entirely different from standardised charging protocols for large series electric cars. An OEM may be able to use developments in his powertrain in series production, but charging is different. We don’t want to invest in something that is just a gimmick.
Mr Mühlon, thank you very much for the conversation!
>> Interview by Sebastian Schaal; translation and copy-editing by Nora Manthey.
0 Comments