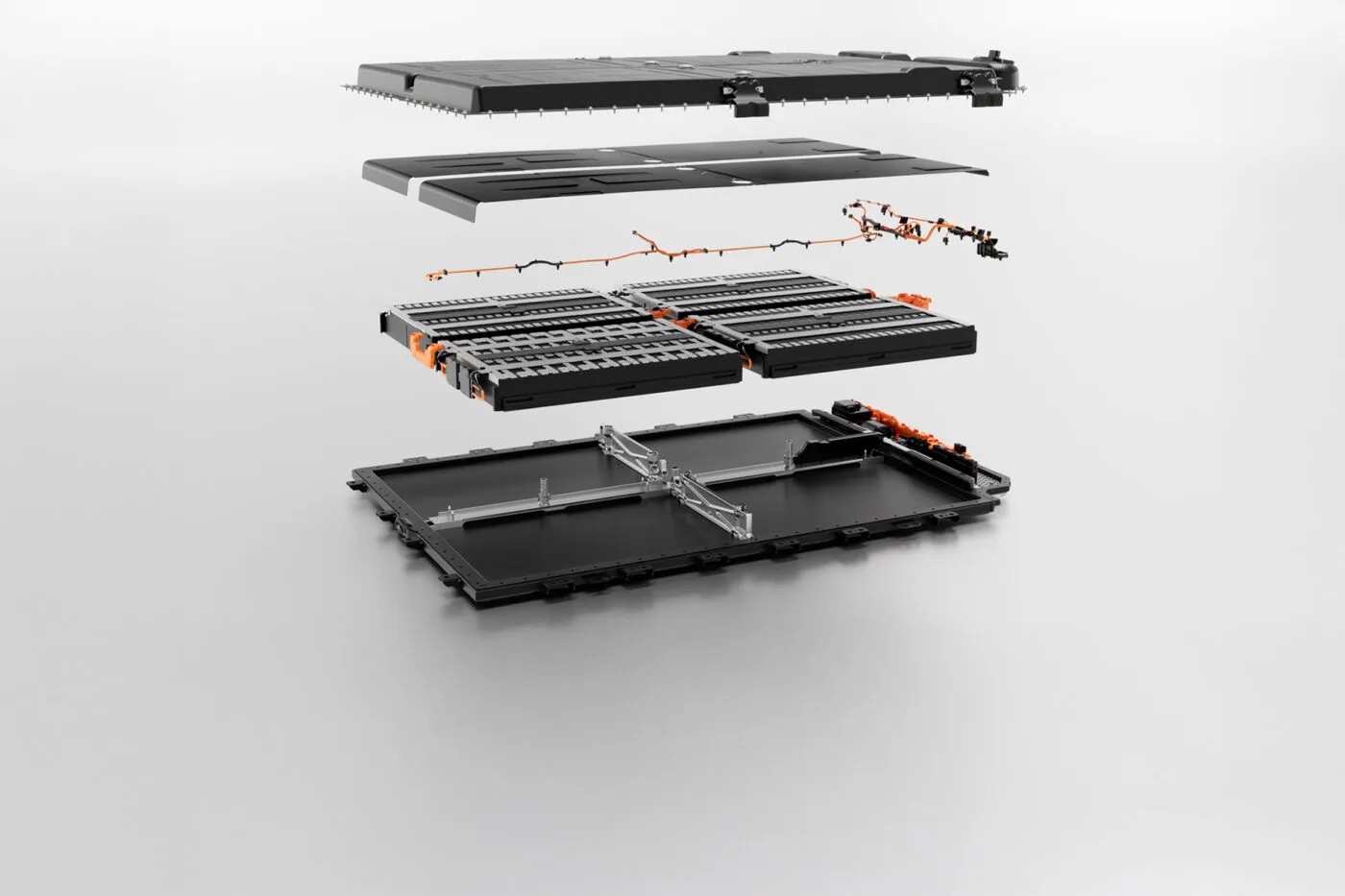
How battery systems can become more sustainable – Eight questions for Hans Beyer from Webasto
Three factors are particularly important for customers when it comes to the ideal electric car battery: the range (energy content in relation to the battery), how quickly the battery can be charged and, indirectly, how much the battery costs – as the most expensive component, it has a noticeable influence on the vehicle price.
In development, however, the matter is far more complex, as many additional factors have to be taken into account. What is the maximum size and weight of the battery pack in the vehicle? How are the battery cells integrated into the pack? How is the safety of the battery and the vehicle ensured in the crash test and beyond? How important is easy repair? How sustainable should the battery be, and what transport routes for the components need to be taken into account? And how easy should the battery be to recycle at the end of its service life?
There is no generally applicable, optimal solution – only the best possible compromise, depending on the desired focus. One example: with modern cell-to-pack concepts, for example, the energy density and the range increased. However, the battery cells are often firmly glued together, and repairing a defective cell is only possible with a great deal of effort, which also makes recycling more difficult. However, if these factors are important, a “classic” battery concept with modules may be more suitable.
In the run-up to the international Advanced Battery Power conference on 2 and 3 April in Aachen, Germany, we spoke to Hans Beyer from the supplier Webasto about the development trends in battery systems. Webasto is not only active in the field of thermal management or vehicle roofs, but is also an important player in the industry when it comes to battery systems.
Mr Beyer, you head the pan-European development team for the system integration of battery cells at Webasto. It is well known that Asian manufacturers are way ahead in terms of cell technology, especially when it comes to industrialisation. Can we Europeans keep up with innovations in battery packs?
In Europe, we have completely different prerequisites for the development and industrialisation of battery packs than we do for cells. Our established ecosystem of automotive suppliers has the necessary development and industrialisation expertise in the areas of mechanics, thermal and electrics/electronics to be innovative and successful here. The decisive factor is to shape the transformation to electric mobility together with car manufacturers.
What role do the properties of a battery cell play when it comes to designing an optimised battery module or pack? So is it an advantage if a manufacturer like BYD can customise its battery cells precisely to its vehicles?
Companies with a high level of vertical integration such as BYD undoubtedly have advantages in terms of time-to-market due to the elimination of external interfaces. However, focussing on in-house cell technology also limits their scope, while car manufacturers and battery system providers such as Webasto, which do not have their own cell production facilities, can draw on the entire portfolio of different cell technologies and formats to create the perfect vehicle-specific fit.
Where are you currently focused in your work? Can it be broken down to the simple formula ‘more energy content, lower costs’?
These are of course two important factors, but by no means the only relevant ones. For example, sacrificing energy density in favour of fast-charging capability can certainly make sense, as a battery with less energy content is then often sufficient, which in turn has a positive effect on costs and resource consumption. That is also an example of how, despite the need to reduce costs, it is crucial that this is done in a smart way and without compromising on quality or safety. For example, the consumption of resources per battery can be optimised through a thorough understanding of the requirements and customised engineering. Short transport routes through production close to our customers – such as at our battery plant in Dangjin (KR) – also save costs and make our products more sustainable.
What role does cell chemistry play in system integration?
The cell is the centrepiece of every battery system. Cell chemistry and format play a key role in defining the electrical, mechanical, thermal and safety requirements for module and pack design. And cell chemistry also ultimately determines the choice of the most suitable cell format. A deep understanding of cell chemistry is thus also essential for battery system providers such as Webasto, for whom battery cells are at first glance ‘only’ purchased or set parts.
Incidentally, I am particularly looking forward to discussing the influence of cell chemistry on the life cycle assessment of a battery pack at Advanced Battery Power on 2 April.
Lithium iron phosphate batteries are on the rise in cheaper, small and compact cars because they are more robust and, above all, cheaper. However, performance at low temperatures is an issue with LFP. This can be remedied with a battery heater, but some manufacturers are saving on this for the low-cost compact cars. Isn’t that saving money at the wrong end? What costs are we talking about here?
Given the large number of technical solutions for thermal management, it is difficult to give a generalised answer to the cost question – but in almost every case, a heating and cooling system adapted to the usage profile pays off, especially with regard to the currently increasing availability of battery cells, which enable charging rates of over 4C with appropriate preconditioning. It is particularly relevant for small cars with LFP batteries to utilise this potential, as a charging time of less than 15 minutes makes a small car with a 50 kWh battery suitable for long journeys. In addition, battery preconditioning technically includes a parking heater, which offers added value, especially for cost-conscious users without a garage parking space. With many years of expertise in thermal management, Webasto can of course score points here.
What are the medium and long-term trends for battery integration in vehicles? Currently, energy density seems to be extremely important, as trends such as cell-to-chassis show. However, the highly integrated and often bonded battery packs are much more complex to recycle. Will there be a rethink?
In addition to energy density, highly integrated packs offer many other advantages and enable savings in materials and production steps, which benefits both the environmental footprint and costs. At the same time, the battery recycling industry is still in the early stages of developing its technologies and capacities. In any case, it will be crucial to anticipate the future skills of recycling partners as early as the product design stage – and this also includes the handling of adhesive bonds. Only intensive collaboration across the entire value chain will produce the overall concepts with the best eco-balance.
Most European manufacturers are focussing on integrating ‘their’ battery into the vehicle in the best possible way – as a competition-defining component. What is your opinion on battery replacement? Does this have a chance with some standardised battery formats, or does the battery optimally integrated into the vehicle remain superior?
Standardisation of the respective battery platforms will certainly continue to gain in importance within the groups. On the other hand, I see cross-group standardisation as realistic at best in special applications such as mobile machines. With the standards of quality and service life of batteries that can now be achieved and the ever shorter charging times, the advantages of battery replacement for cars are shrinking noticeably.
During your time at the Technical University of Munich in Germany, you also co-founded a startup that develops and produces customised skis. How can you apply your experience in startup management to your current tasks in battery development?
With our own startup, we first had to establish a new market segment for Europe and build up a functioning supply chain as an underdog. When I started at Webasto Batteries in 2018, we first had to establish our right to play and secure the supply of suitable battery cells. Both times, a pioneering spirit, perseverance and a certain degree of resilience were required – and all of this will also be an advantage for the future of electric mobility with its ongoing turbulent technical, economic and social developments.
The interview is part of electrive’s media partnership with ‘Advanced Battery Power’ from 1 to 3 April 2025 in Aachen, Germany. Hans Beyer’s presentation will take place on 2 April at 10:55 a.m. in the Europa-Saal.
0 Comments