Soitec opens semiconductor factory with “SmartCut” technology
Setting this so-called SmartCut technology aside for a minute, the new factory opened today spans 2,500 square metres. At final capacity, Soitec expects about 400 staff to produce half a million SiC wafers annually.
A technological interlude – semiconductors ensure that power electronics in a system work particularly energy-efficiently. While these chips were traditionally made of high-purity silicon, silicon carbide (SiC) is increasingly replacing silicon. ZF and Wolfspeed or Bosch are among the companies following a similar approach in Europe.
SiC semiconductor efficiency lays in their higher conductivity and higher switching frequencies compared to silicon chips. Only around half as much energy is lost as heat which increases the range of electric cars. Since less heat is emitted and the SiC components can withstand higher temperatures, the power electronics cooling system can be smaller. This saves energy and reduces weight and costs thanks to the more compact cooling systems.
Soitec also claims these benefits. The company adds the mentioned ‘SmartCut’ technology for the wafers – a thin slice of semiconductor material constructed of various substances – would allow each substrate to be used ten times. This reduces CO2 emissions during manufacturing by 70% compared to monocrystalline SiC substrates, according to Soitec.
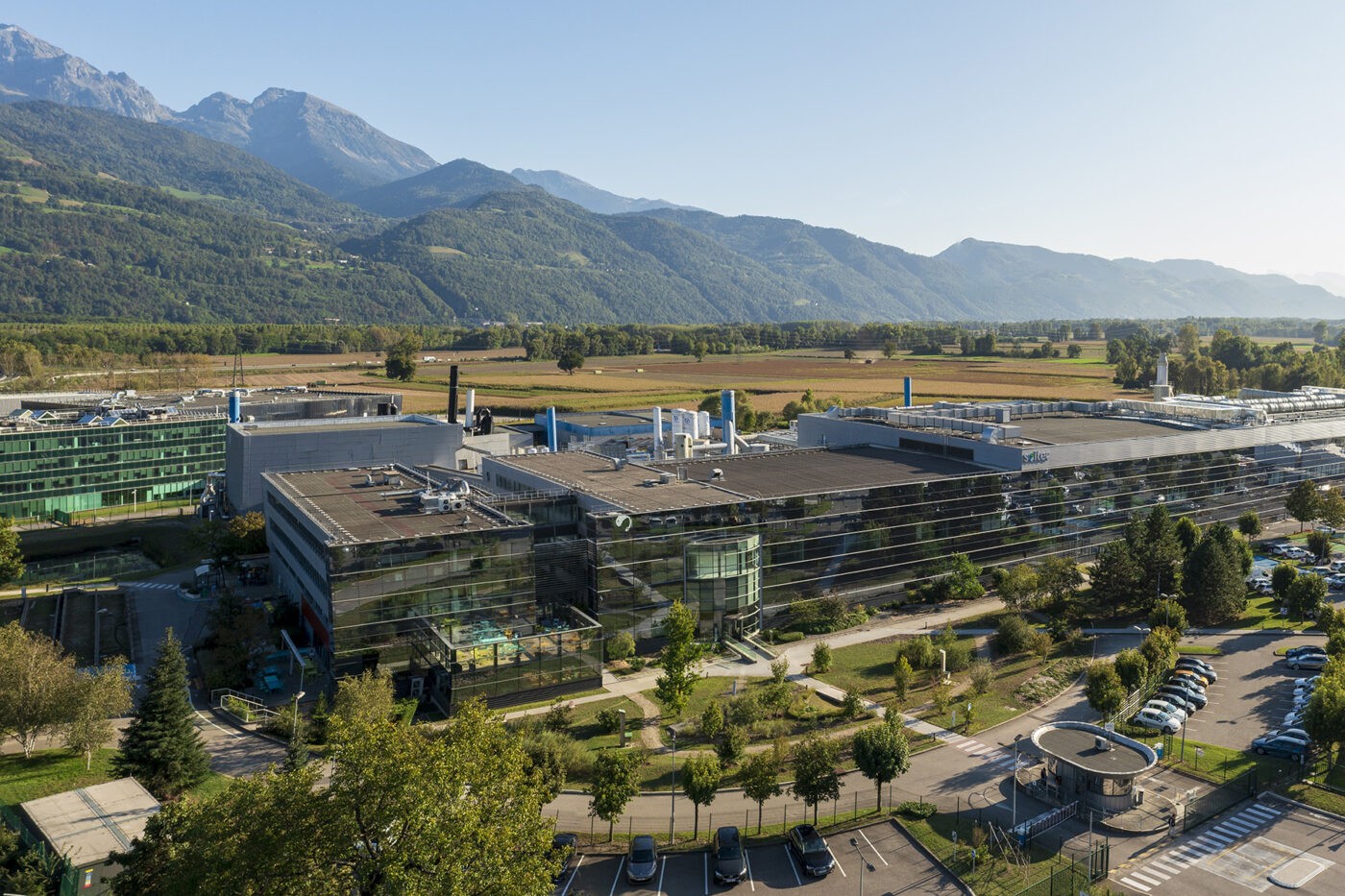
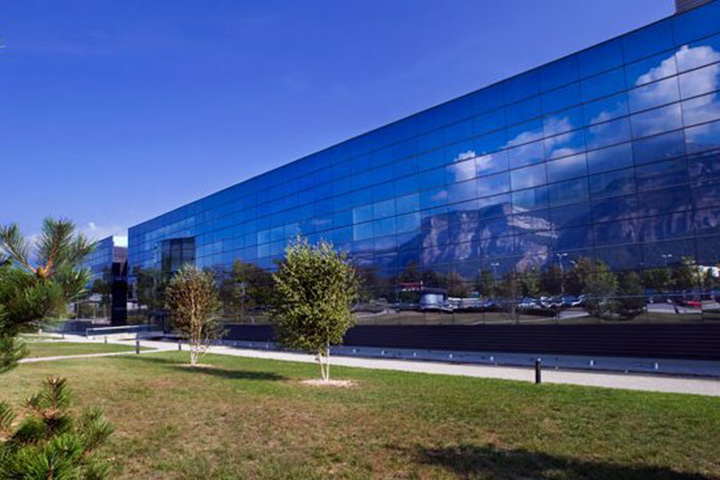
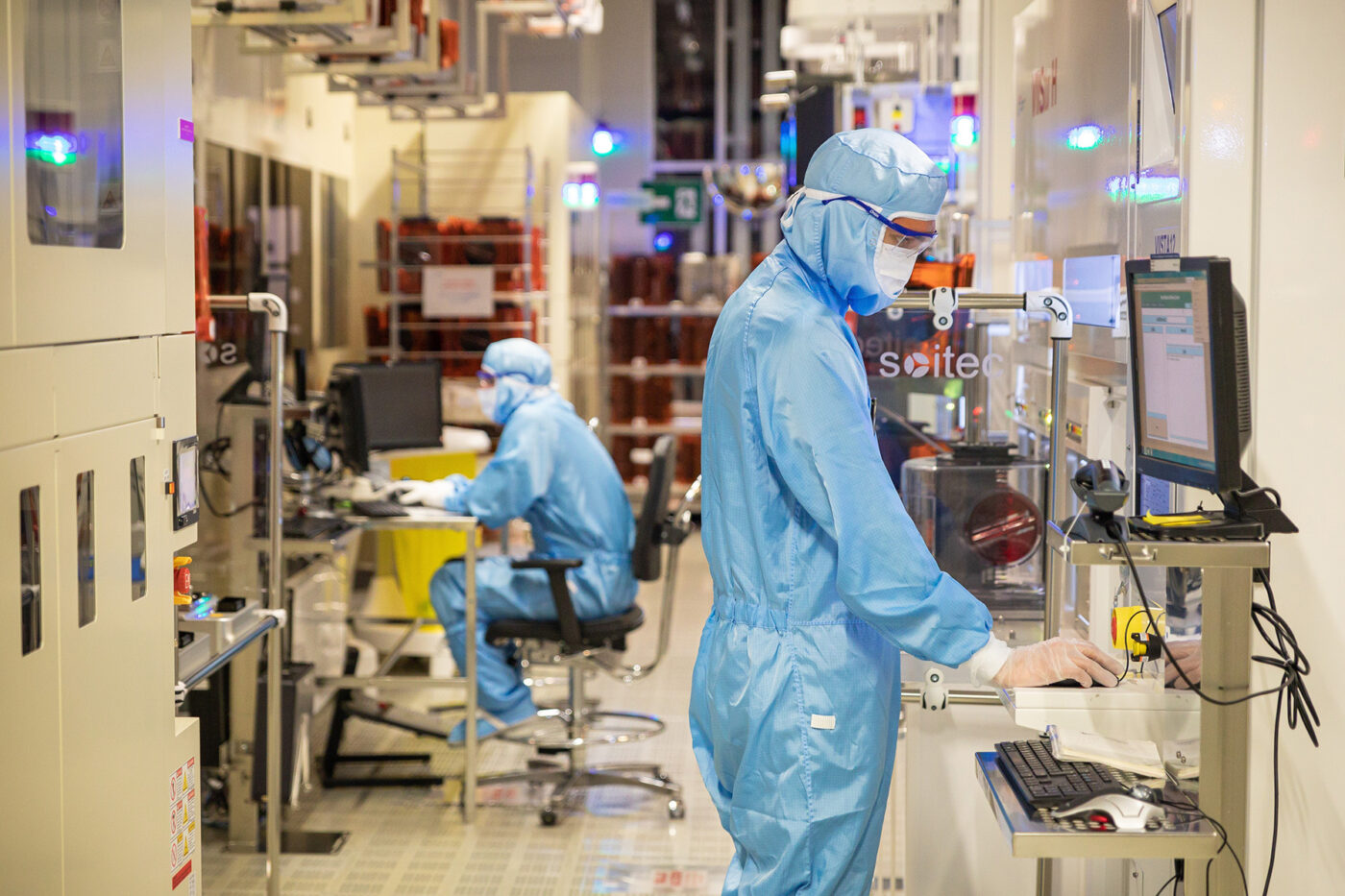
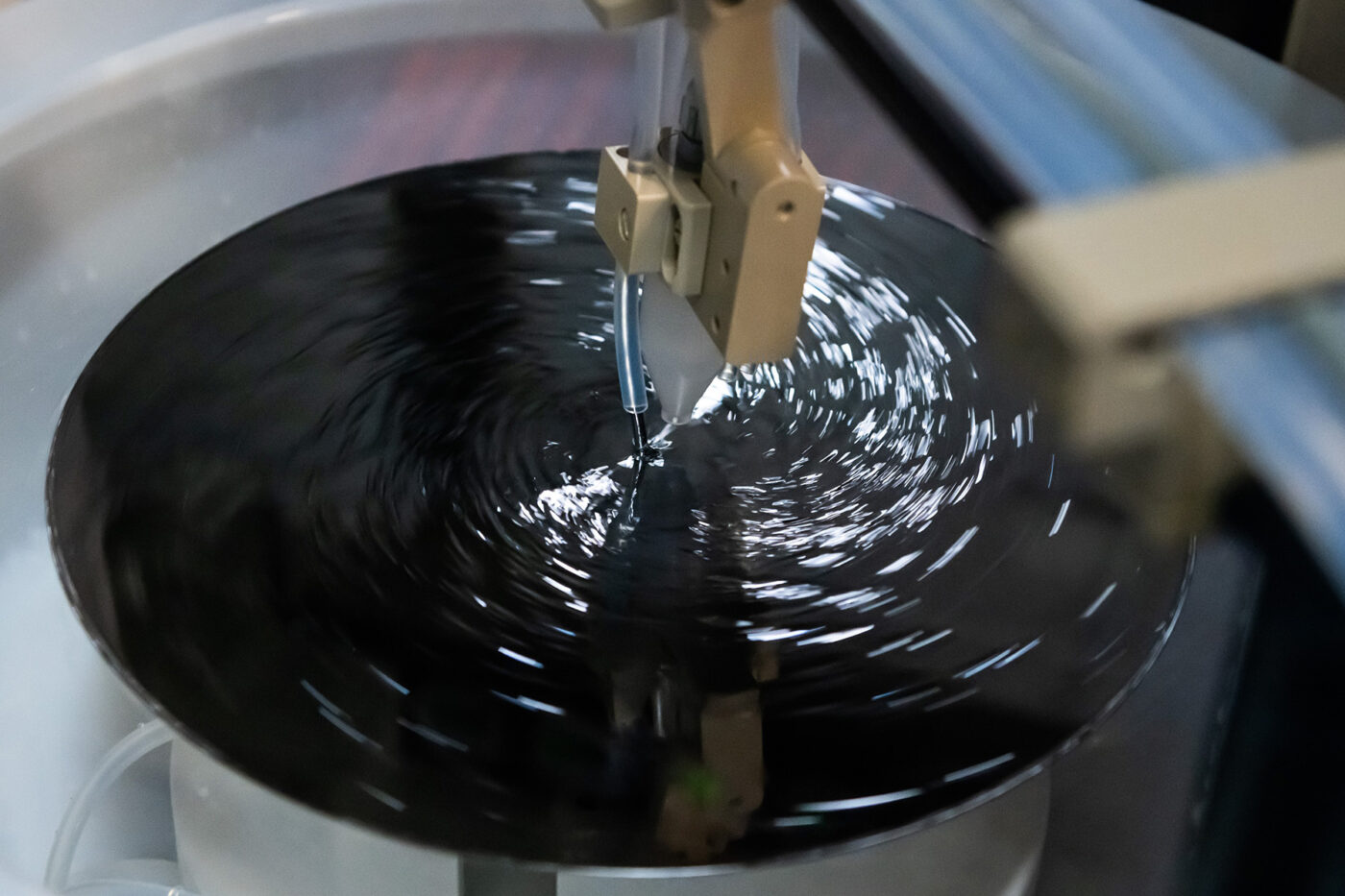
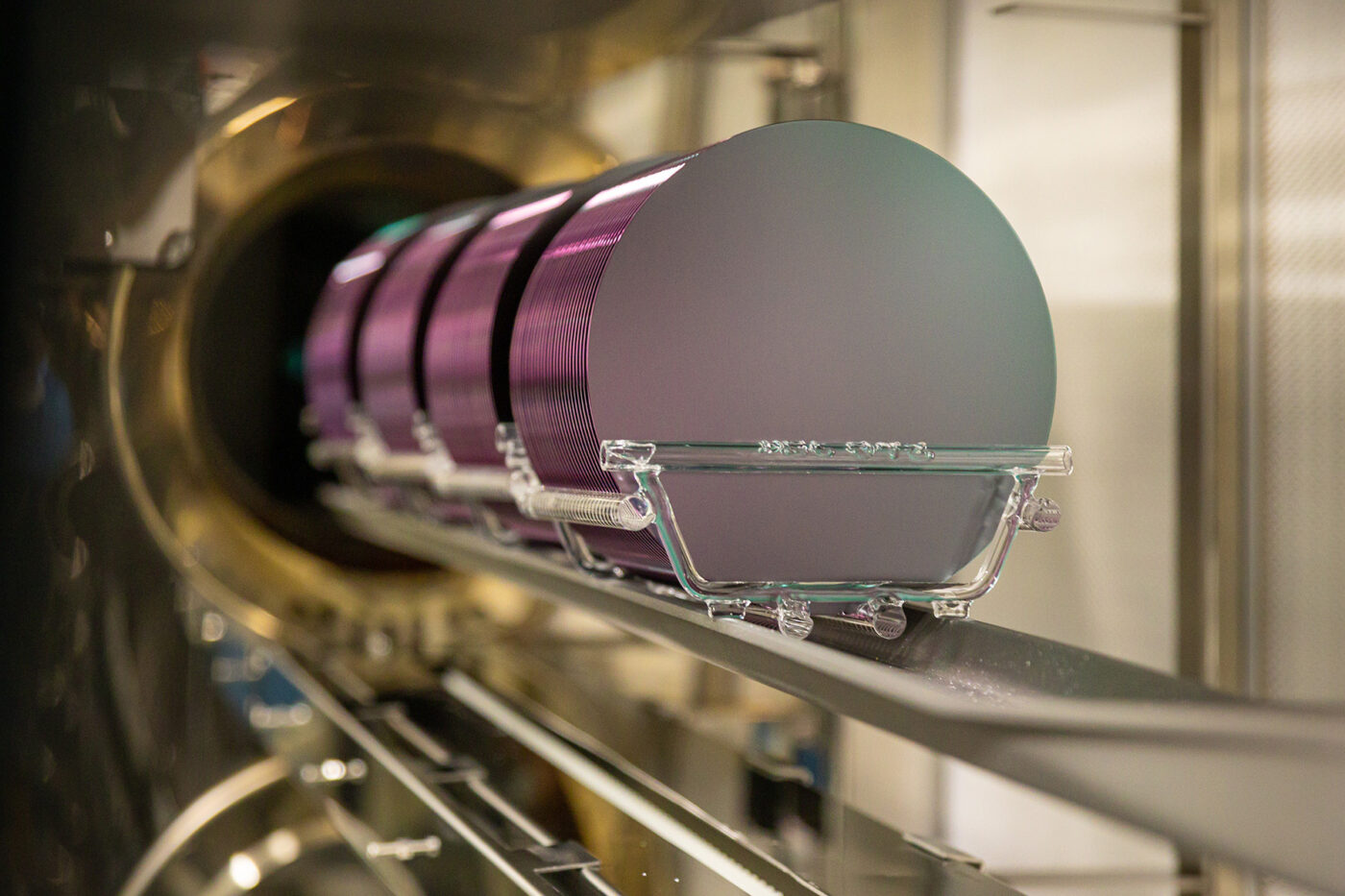
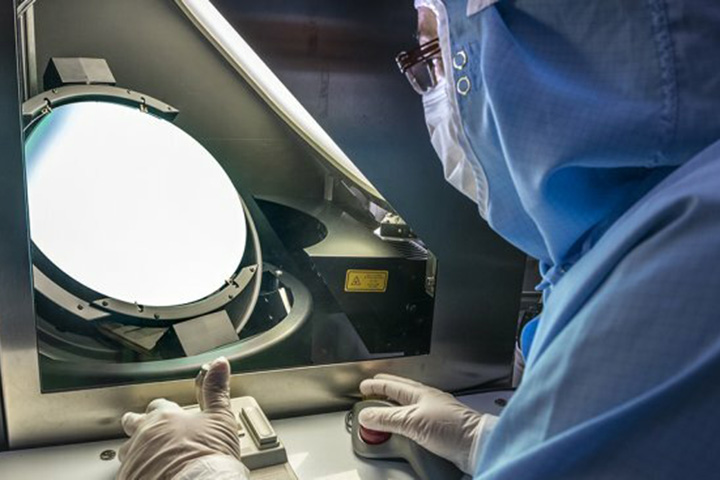
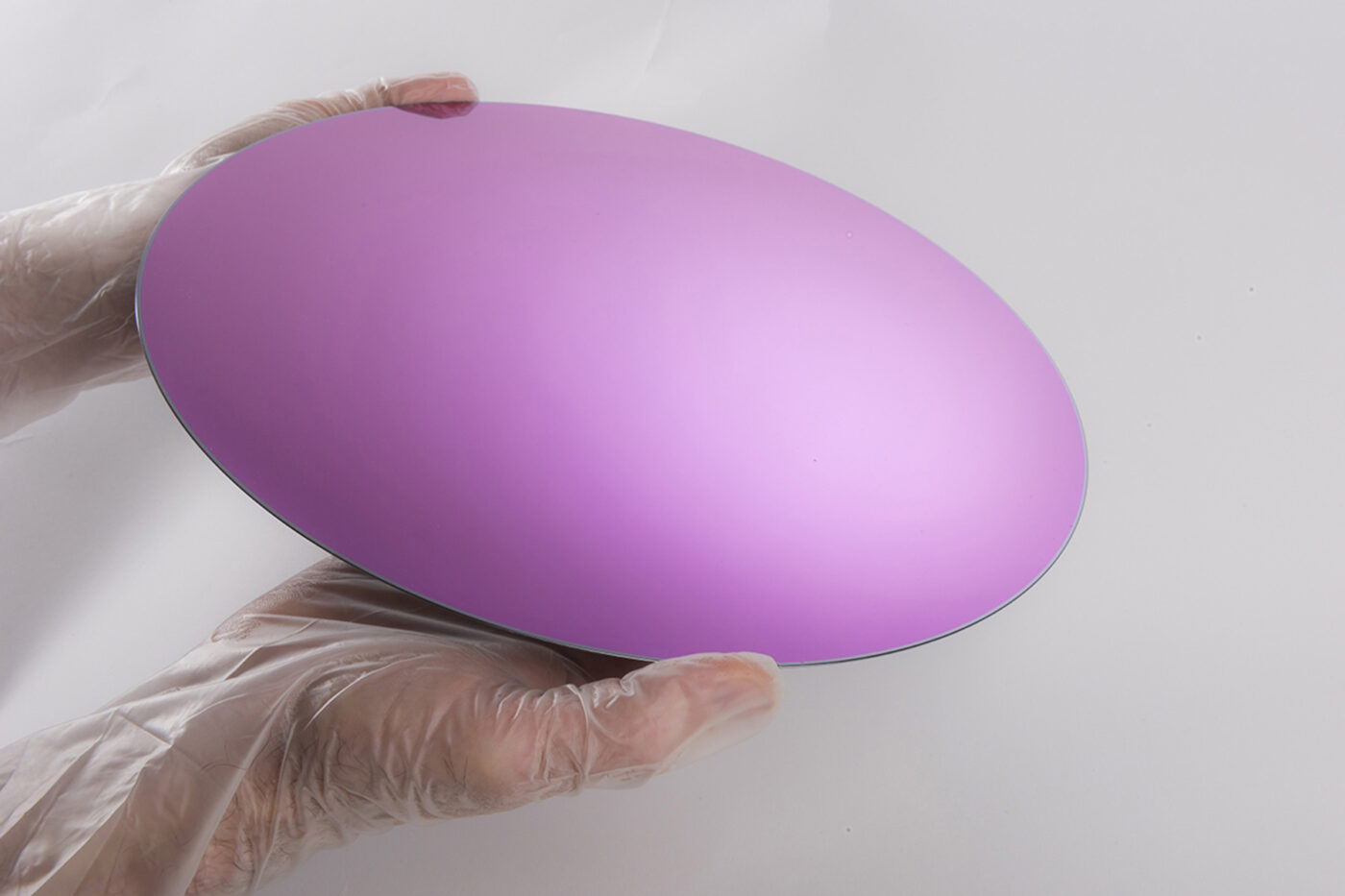

While the technology remains based in SiC, the company also claims it would enable electric vehicles to achieve ranges above 500 km, compared with an average of 350 km for cars using silicon IGBT alternatives.
Soitec began developing the technology in 2020 in partnership with CEA-Leti and has received financial support from the French state, the region, local authorities and the European Union.
The new factory also received political support. Thierry Breton, European Commissioner for the Internal Market and Roland Lescure, French Minister Delegate for Industry, were present at the opening.
Pierre Barnabé, the Soitec CEO, said, “This plant will enable us to meet growing demand for silicon carbide and achieve a 30% market share by 2030 while helping to make electric mobility more efficient and affordable.”
1 Comment