Mercedes-Benz Trucks electrifies its factory logistics
To electrify its local supply chains, several of the Mercedes-Benz Trucks’ logistics partners to and from its Wörth plant are taking over a dozen eActros 300s. The company also wants to pass on its experience to other companies for which it is consulting services.
The Wörth site is the largest truck assembly plant of Mercedes-Benz Trucks and, with around 10,000 employees, the second largest employer in the region. The plant manufactures the Actros, Arocs and Atego series, and the Econic, Unimog and Zetros special trucks all roll off the plant’s production line. The electric eActros 300/400 has also been built at the plant since 2021, and the eEconic variant since 2022. The eActros 600 electric heavy-duty truck, unveiled in October 2023, will go into series production there at the end of 2024.
Mercedes-Benz Trucks also aims to use its electric trucks in its supply chain. As a first step, 17 logistics partners are taking delivery of 20 eActros 300 tractor units for use in inbound logistics in Wörth. This refers to delivery traffic from suppliers or sister plants. Outbound logistics is the transportation of finished products from the assembly line to the customer.
The truck maker has also just revealed that its eActros 300 tractor unit is now also available as a lowliner version – initially for selected customers in plant logistics – “which is particularly suitable for use with mega trailers and in automotive logistics”, as Mercedes Benz Trucks states. The lowliner can also score points for volume transports that require an interior height of up to three meters. From next year, the eActros 300 Lowliner will be produced in small series and will be available to order from January 2024
Twelve eActros already handed over
For deliveries to and from Wörth, the first twelve eActros were received by the truck group’s logistics service providers in the last few days. From the first quarter of 2024, they will complete around 50 transports daily in and around the Wörth plant. The eight other vehicles will follow soon. The 20 eActros will be operated by 17 different companies, including DHL Freight to and from Bonn, and Schenker between the plant and Frankfurt am Main.
“Today, electric trucks can cover the majority of delivery routes over short and medium distances,” comments Karin Rådström, CEO of Mercedes-Benz Trucks. “We want to leave the smallest possible CO2 footprint across the entire value chain. This also includes the issue of inbound logistics at our Wörth plant. We are delighted that many of our logistics partners are now switching to the all-electric Mercedes-Benz eActros and driving the transformation of the industry forward with us. For some of our logistics partners, this marks their entry into electromobility.”
The federal German government is contributing three million euros to the financing of the Wörth project via the KsNI program. This is because the investment requirements go beyond the vehicles including the appropriate charging infrastructure for trucks. To this end, around 30 charging stations, including stations with the new MCS megawatt charging standard, are initially to be installed on the site. They are planned at “key points for delivery traffic in the immediate vicinity of production”.
A total of eight charging stations should be available by 2023. Following the inauguration of a pilot charging station this summer, the truck manufacturer plans to install five more charging stations in various delivery areas within the plant over the course of the month, as well as two charging stations in the truck parking lot in front of the plant gate.
In theory, the electric trucks should be charged while its freight is unloaded. As deliveries to the plant are made according to the just-in-time principle, there can be no delays at the unloading ramp. At the same time, the trucks’ journey times are so tightly timed that they are bound to a strict schedule. If the system works perfectly with charging during unloading, the drivers would not have to schedule additional downtime for charging the battery and can resume their route immediately after delivering the parts.
The eActros 300 can be charged with up to 160 kW. It takes just over an hour to charge the three installed batteries with a total of 300 kWh from 20 to 80 per cent at a DC fast-charging station with 400 amps of charging current. As MCS chargers are also planned, it stands to reason that the eActros 600 will also be integrated into the plant logistics in time. The electric heavy-duty truck can be charged from 20 to 80 per cent in “well under 30 minutes” despite having a much larger battery with more than 600 kWh.
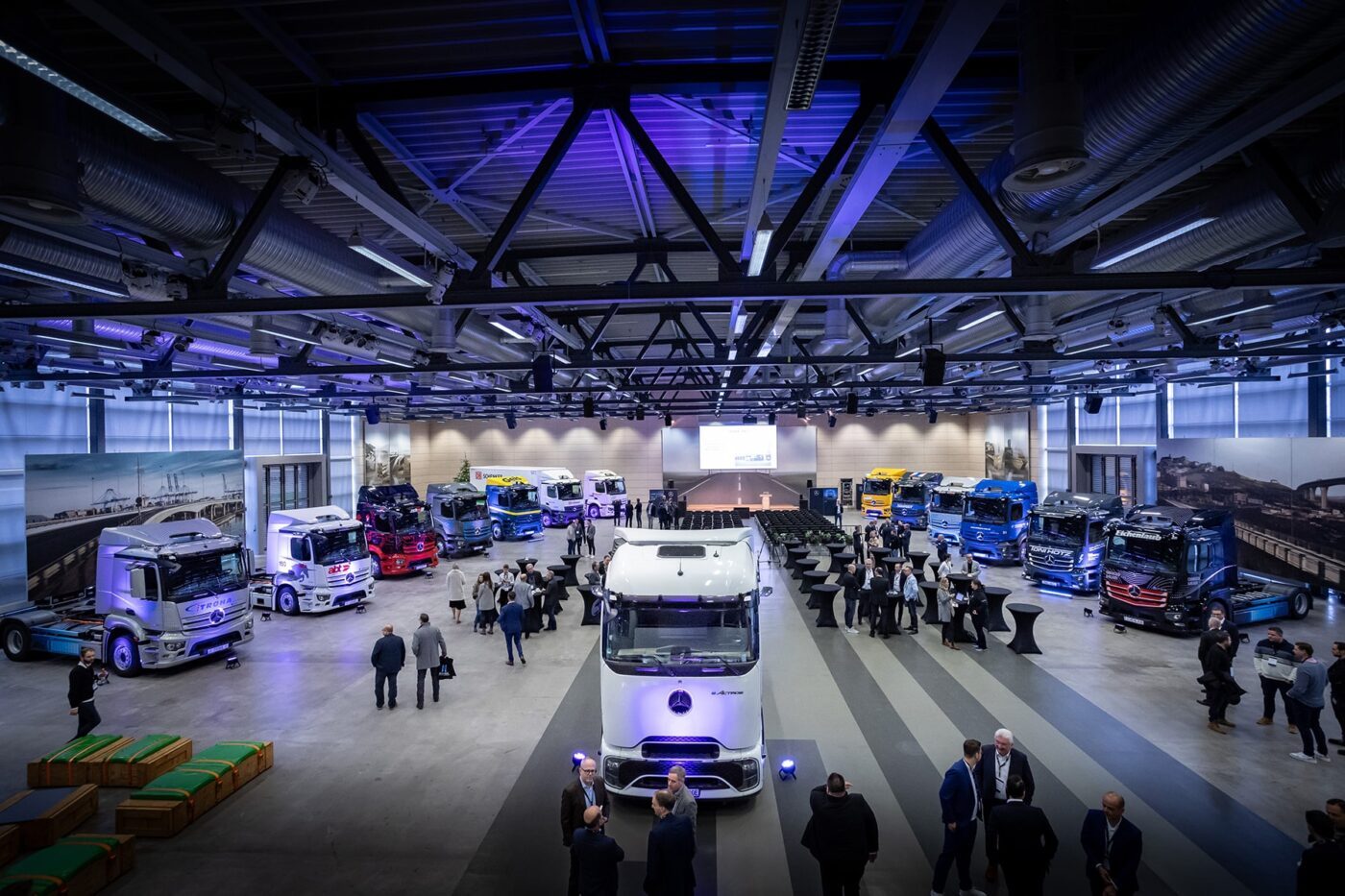
It is not clear from the announcement which charging stations will be used in the company’s own charging park for suppliers. Daimler Truck has been able to determine which model will be suitable for this application itself over the past few months: In July, the demo charging park at the Wörth plant was put into operation. The facility is intended to enable customers to test charging stations and concepts from various manufacturers and to develop customized charging solutions for their own needs with the help of experts on site. This expertise can, of course, also be used for the company’s own fleet requirements.
As with the demo charging park, the company’s main aim with its own delivery logistics project is to demonstrate to the outside world how battery-electric trucks can already be used today. Both logistics and charging infrastructure experts from Mercedes-Benz Trucks have been in close contact with the partner companies involved right from the start – “on topics that go far beyond pure vehicle procurement”, the initiators explain. In addition to the required charging infrastructure at the logistics hubs, the main focus here was on the precise analysis of the incoming and outgoing routes for supplying the production site and planning the charging points.
The Group now wants to make the know-how gained available to other industrial companies. To this end, Mercedes-Benz Trucks is launching a consulting program called ELA (“Electrified Logistics Accelerated”), specifically designed to help electrification plant logistics.
“With the project for the electrification of plant logistics at the Wörth production site, we have done real pioneering work together with our colleagues,” says Andreas Scharff, Head of eMobility Sales and Dealer Network Development Mercedes-Benz Trucks. This makes it all the more important now to share this expertise with other industrial companies, thus fueling the transformation to sustainable logistics and making a joint contribution to effective CO 2 reduction. “With our ELA program, we are therefore deliberately expanding our
consulting and service portfolio towards industrial companies,” says Scharff.
Across the Atlantic, Daimler Truck North America has also just announced a project to electrify its plant logistics in the USA. Initially, four Freightliner eCascadia semitrailer tractors will be used around the plant in Portland.
Translated by electrive.com
0 Comments