Daimler Truck and Linde show fuelling solution for liquid hydrogen
Compared to conventional refuelling technology with liquid hydrogen (LH2), the new process uses a new sLH2 pump to increase the pressure of the liquid hydrogen slightly. The method turns hydrogen into subcooled liquid hydrogen (sLH2). According to Daimler Truck, it will be a “very robust fuelling process,” which results in lower energy losses during refuelling than conventional LH2 processes. In addition, no data transfer between the refuelling station and the vehicle is necessary, further reducing the complexity of the refuelling process.
The advantages of LH2 and sLH2 over gaseous hydrogen are well known. The energy density is higher, allowing trucks to cover more distance between refuelling. As “only” a liquid is refuelled, the process is faster than with the gas. Daimler Truck also expects lower costs and greater energy efficiency.
The sLH2 refuelling station that has now opened at the Daimler Truck plant in Wörth, Germany, is open to the public and will be used by selected logistics customers for initial customer trials with the Mercedes-Benz GenH2 Truck from mid-2024. According to the manufacturer, refuelling a 40-tonne truck with 80 kilograms of liquid hydrogen will take “about 10-15 minutes.” Other truck manufacturers specify a similar refuelling time for their fuel cell models with gaseous hydrogen. However, in those cases, less than 80 kg of hydrogen is usually refuelled during that time, which is insufficient for up to 1,000 kilometres – as is the case with Daimler Truck. Daimler Truck demonstrated this range in a record-breaking drive in September.
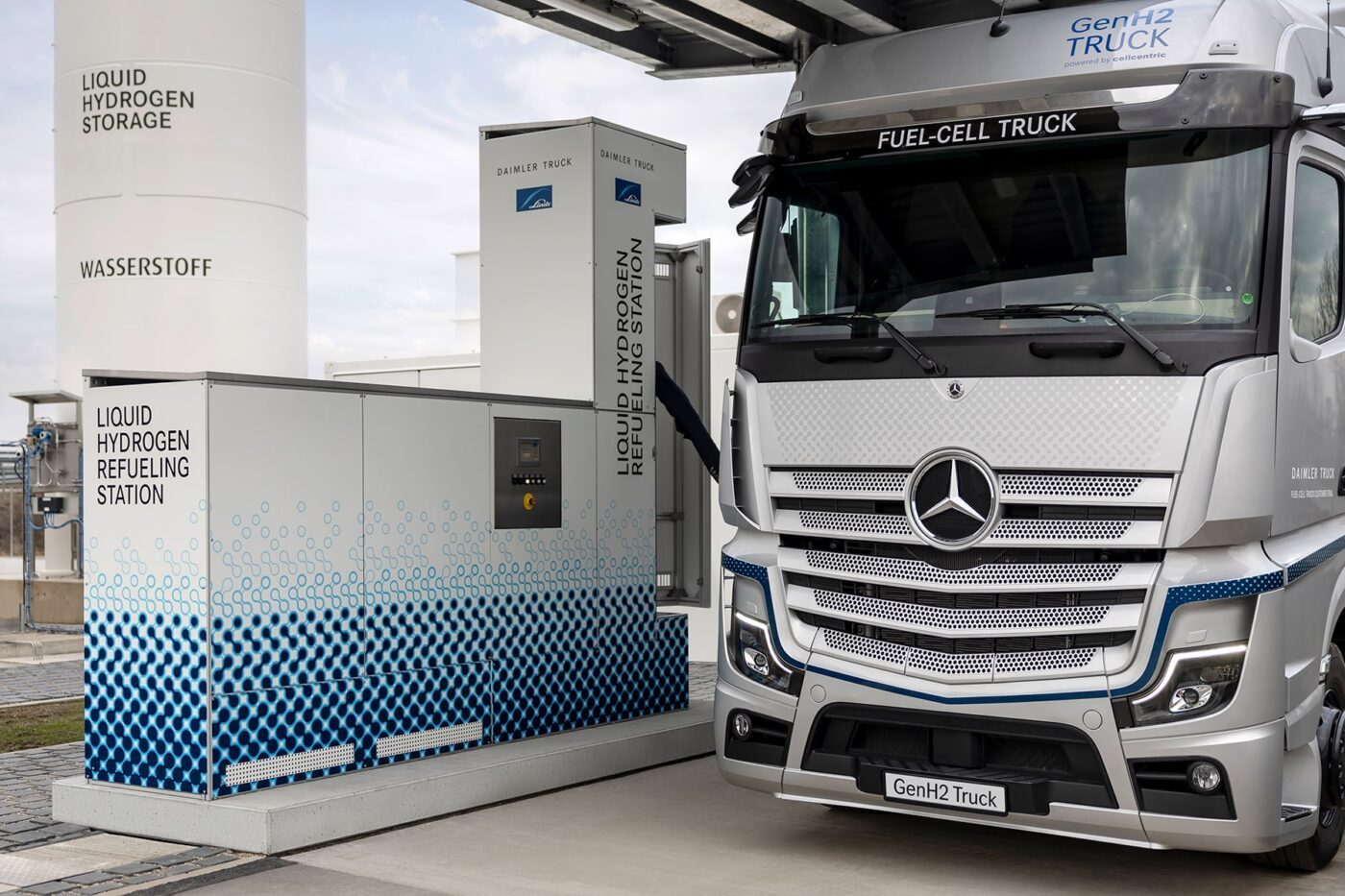
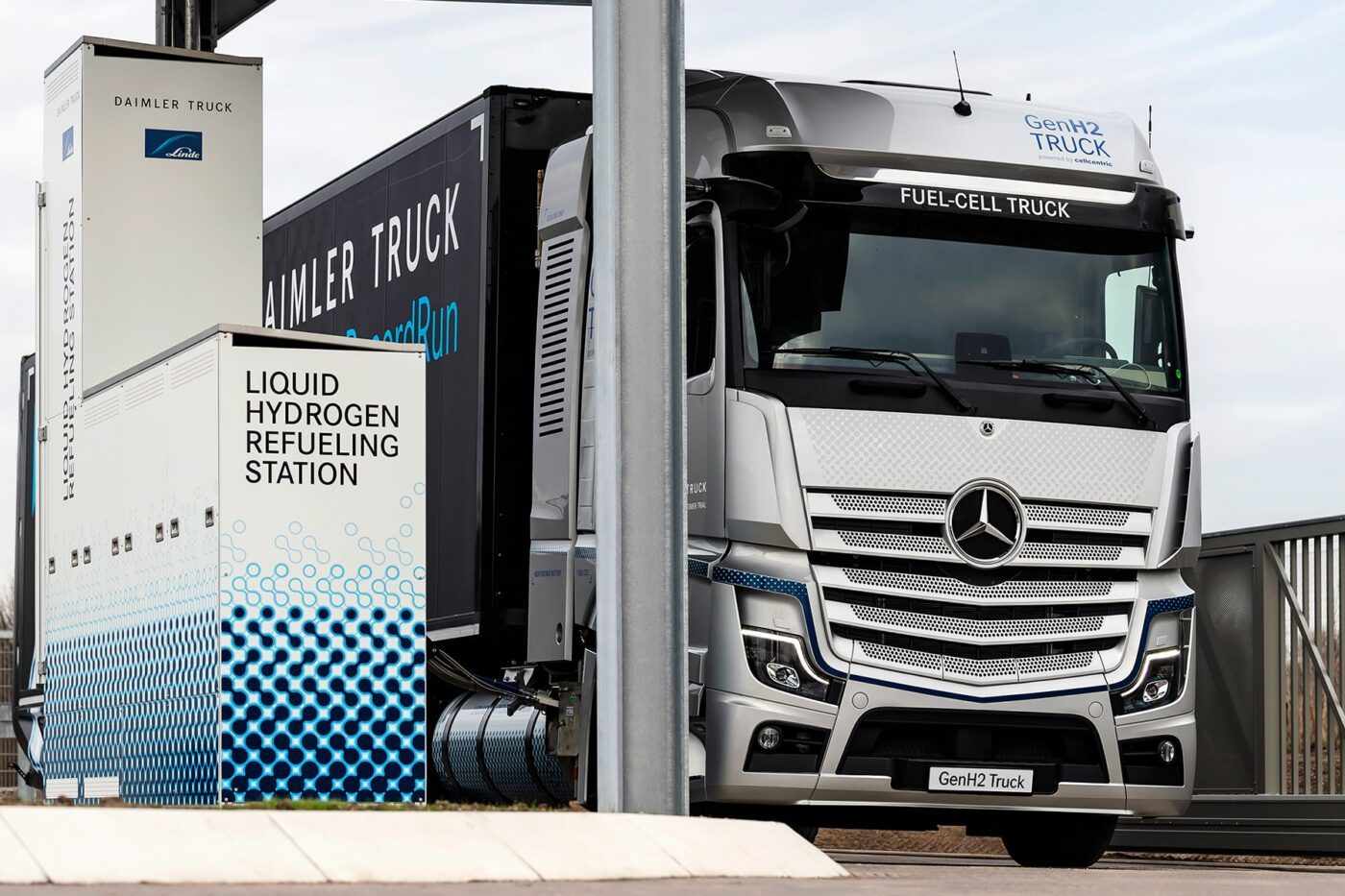
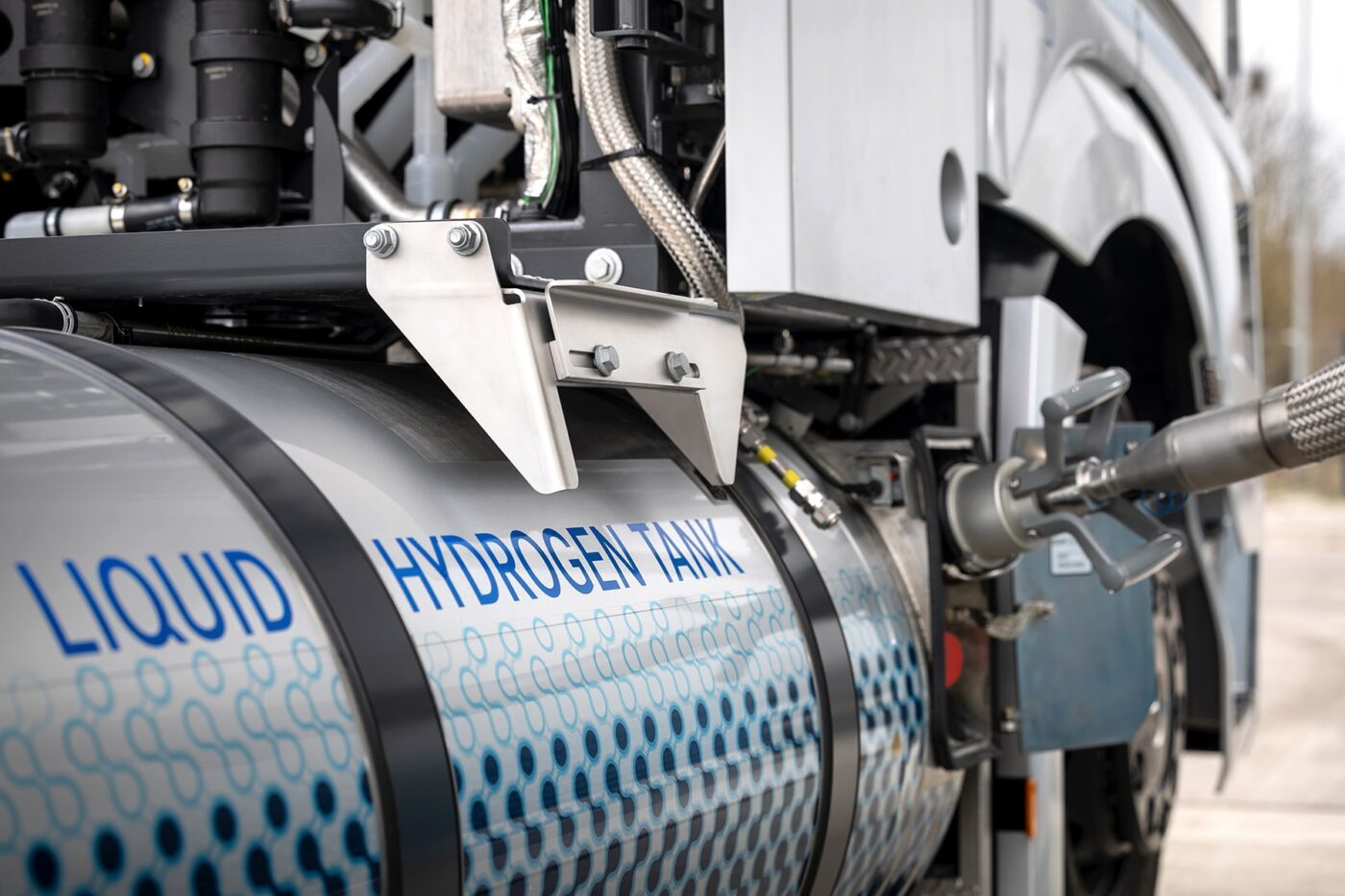

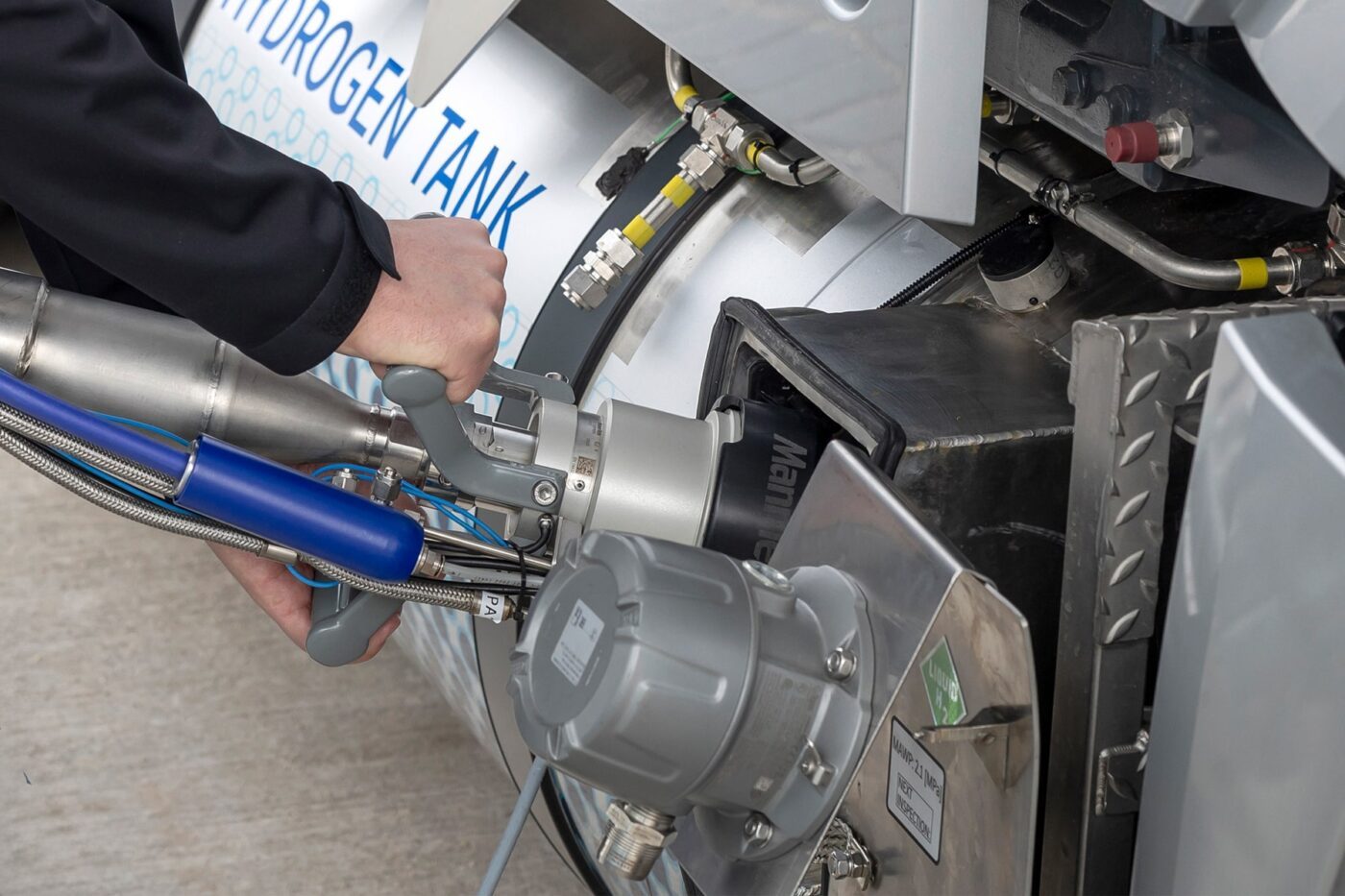
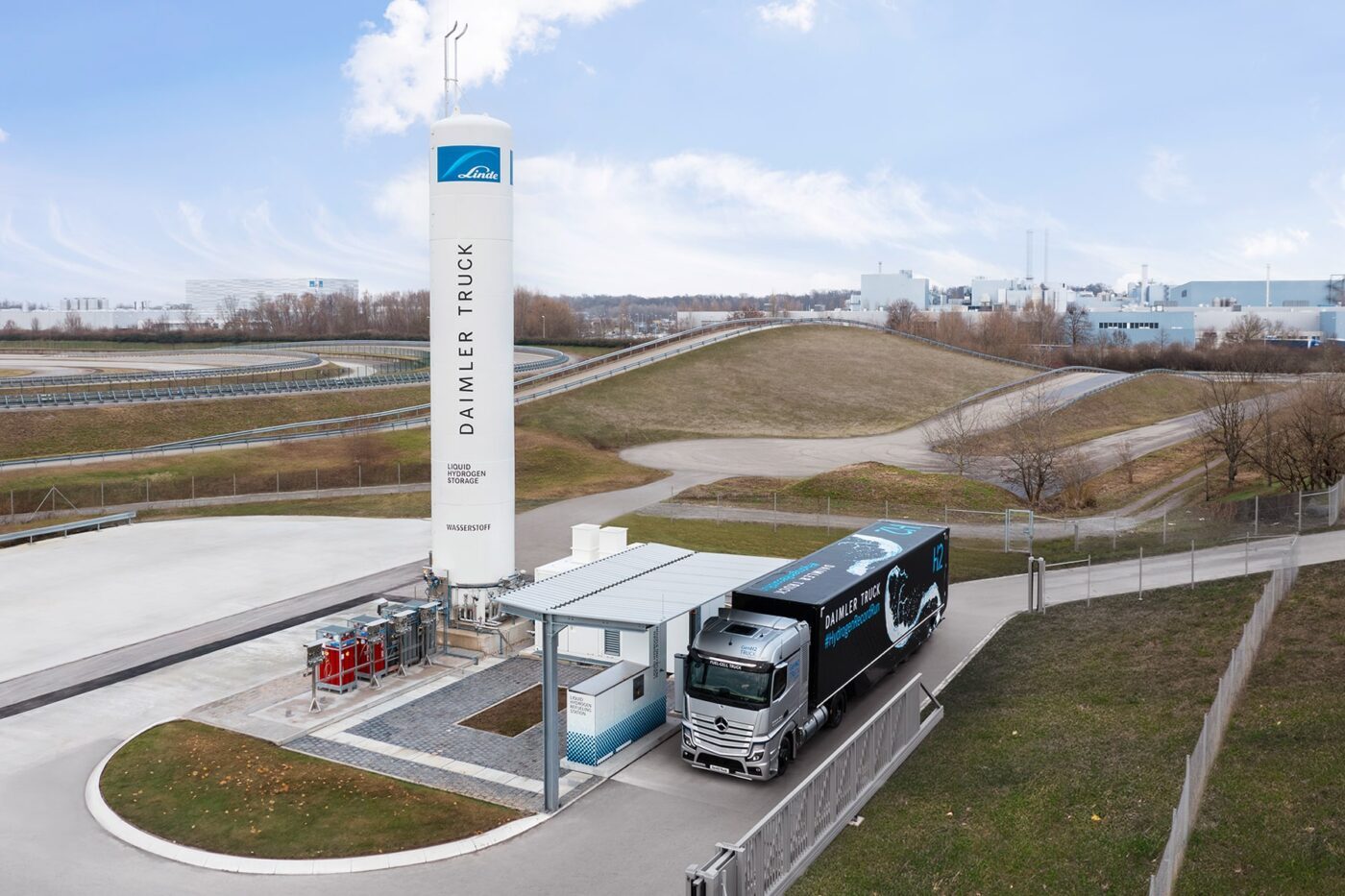
Another potential advantage of a liquid hydrogen refuelling station is that as the gaseous hydrogen does not have to be compressed after each refuelling process, the following vehicle can be refuelled directly – as with diesel. The filling station in Wörth is designed for a capacity of 400 kilograms of hydrogen per hour – in other words, the refuelling capacity of five trucks. With a refuelling time of ten to 15 minutes, there is little time left to re-park. The liquid hydrogen storage tank has a capacity of four tonnes, which is enough for around ten hours of continuous refuelling – if it is refilled in between, eight tonnes can be sold per day.
In the TCO-driven world of logistics, costs are also a hugely important factor. A lot of energy is required to compress hydrogen (which is why 350-bar hydrogen for commercial vehicles is generally cheaper than the even more energy-intensive 700-bar hydrogen). However, cooling LH2 down to -253 degrees Celsius also requires energy. According to Daimler Truck, the sLH2 technology – including all the components – will reduce the investment needed for a hydrogen refuelling station by a factor of two to three, with operating costs being “five to six times lower.” Expressed in concrete figures: the sLH2 refuelling station in Wörth am Rhein will achieve an energy consumption of 0.05 kWh/kg – allegedly 30 times less energy than a refuelling station with gaseous hydrogen.
Daimler and Linde are making the technology available to all interested parties via an ISO standard to establish a common refuelling standard for hydrogen-powered trucks. However, no other truck manufacturer has been as openly committed to liquid hydrogen as Daimler Truck. But for the development of the vehicles for the fuel cell electric drive itself, it makes no difference whether the hydrogen in the vehicle is stored in gaseous or liquid form. It thus depends on the infrastructure the manufacturer relies on. And in terms of the number of refuelling stations, gaseous hydrogen is currently far ahead, regardless of the advantages of LH2 in terms of energy density.
To make sLH2 the standard, Daimler Truck and Linde Engineering offer a “high level of transparency and openness around the relevant interfaces of the jointly developed sLH2 technology.” Daimler Truck and Linde Engineering are now calling on other OEMs, infrastructure companies and associations to apply the new liquid hydrogen standard and thus establish a global mass market for the process.
“Zero-emission transport needs three factors: the right battery-electric and hydrogen-powered vehicles, the required infrastructure network and cost parity for ZEVs compared to diesel trucks,” says Daimler Truck Board Member Andreas Gorbach, responsible for Truck Technology. “In terms of hydrogen infrastructure, we are reaching a major milestone today: With sLH2, hydrogen refuelling becomes as convenient as today’s refuelling with diesel. It takes about 10 to 15 minutes to fuel our Mercedes-Benz GenH2 Truck for a range of more than 1,000 kilometres.”
Jürgen Nowicki, Executive Vice President of Linde plc and CEO of Linde Engineering, adds: “Subcooled liquid hydrogen considerably increases the efficiency of hydrogen refuelling systems. This and further advantages make sLH2 a practical, CO2-neutral alternative to diesel in the heavy-duty vehicle sector. The technology we have developed with Daimler Truck will help pave the way for the development of a robust refuelling network, which is essential to keep vehicles moving and supply chains intact.”
1 Comment