VWGC commissions battery recycling pilot plant
VW’s Group Components division has commissioned a pilot plant for recycling batteries in Salzgitter. With the plant, which is to be scalable to higher capacities, Volkswagen wants to recover valuable raw materials and use them in new batteries.
According to VWGC, with the start of the pilot operation, the group realises “another committed step towards sustainable end-to-end responsibility for the entire value chain of the electric vehicle battery”. Despite generic PR phrasing, the company also provided specifics for their plans: valuable raw materials such as lithium, nickel, manganese and cobalt are recovered in a closed cycle with a “recycling rate of more than 90 per cent in the future”. Aluminium, copper and plastics are also to be recycled.
According to VW, the pilot plant is currently designed for a capacity of 3,600 battery systems per year (or about 1,500 tonnes) because there are not enough batteries worth recycling yet. Only batteries that are no longer suitable for second-life applications are recycled there – VWGC mentions its flexible, fast charging columns or mobile charging robots here, for example. “Larger volumes of battery returns are not expected until the late 2020s at the earliest,” Volkswagen said in the statement. Therefore, they designed the plant to be “scaled up to handle larger quantities as the process is consistently optimised”.
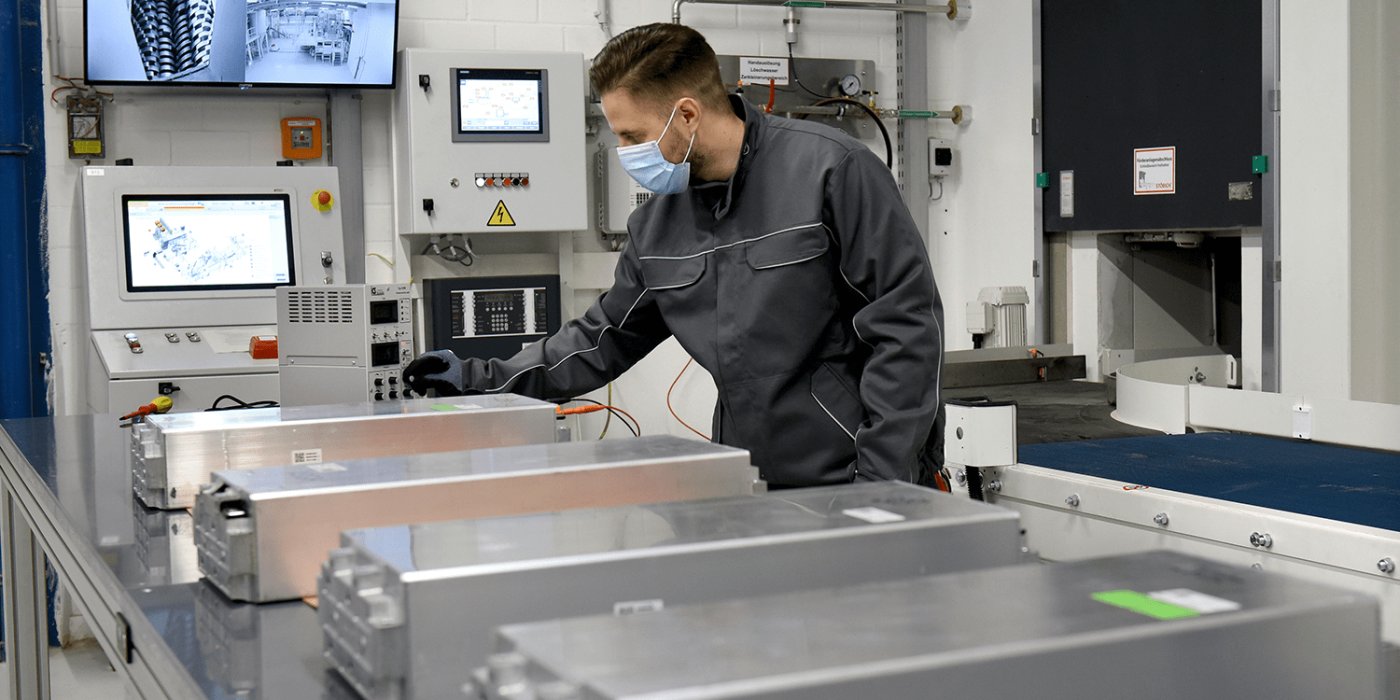
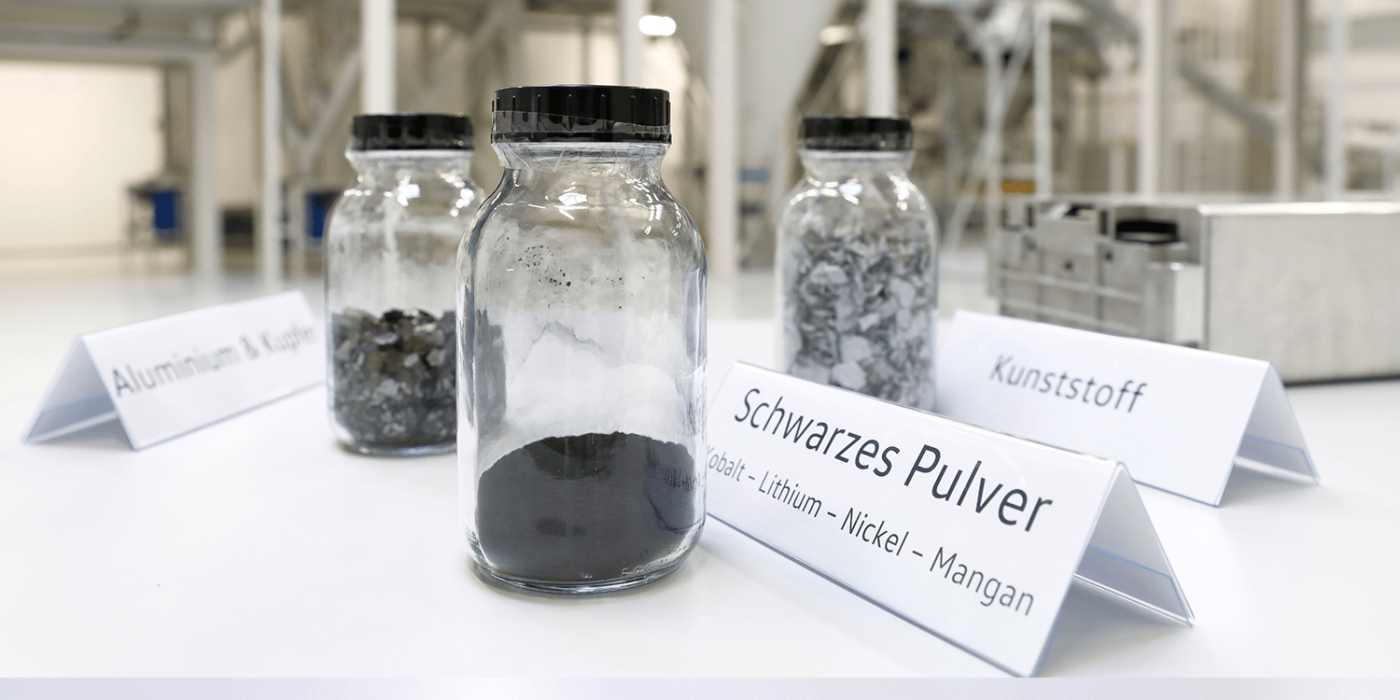
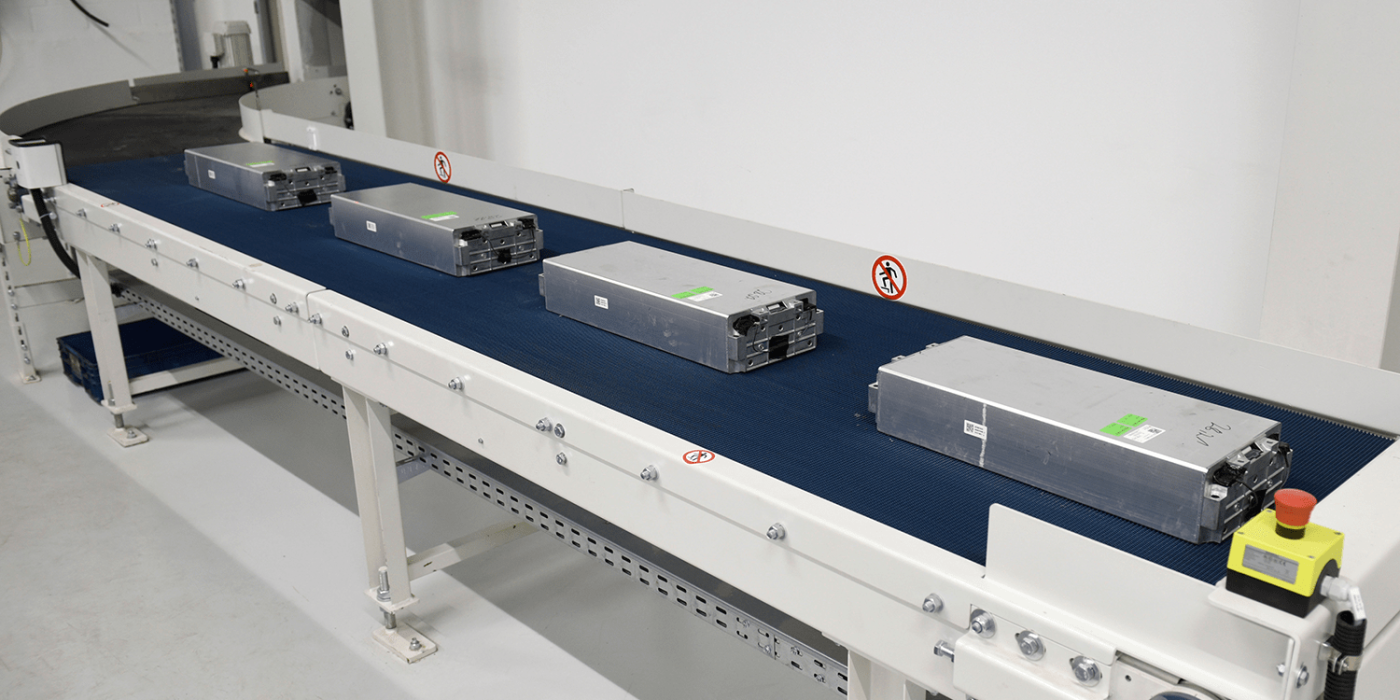
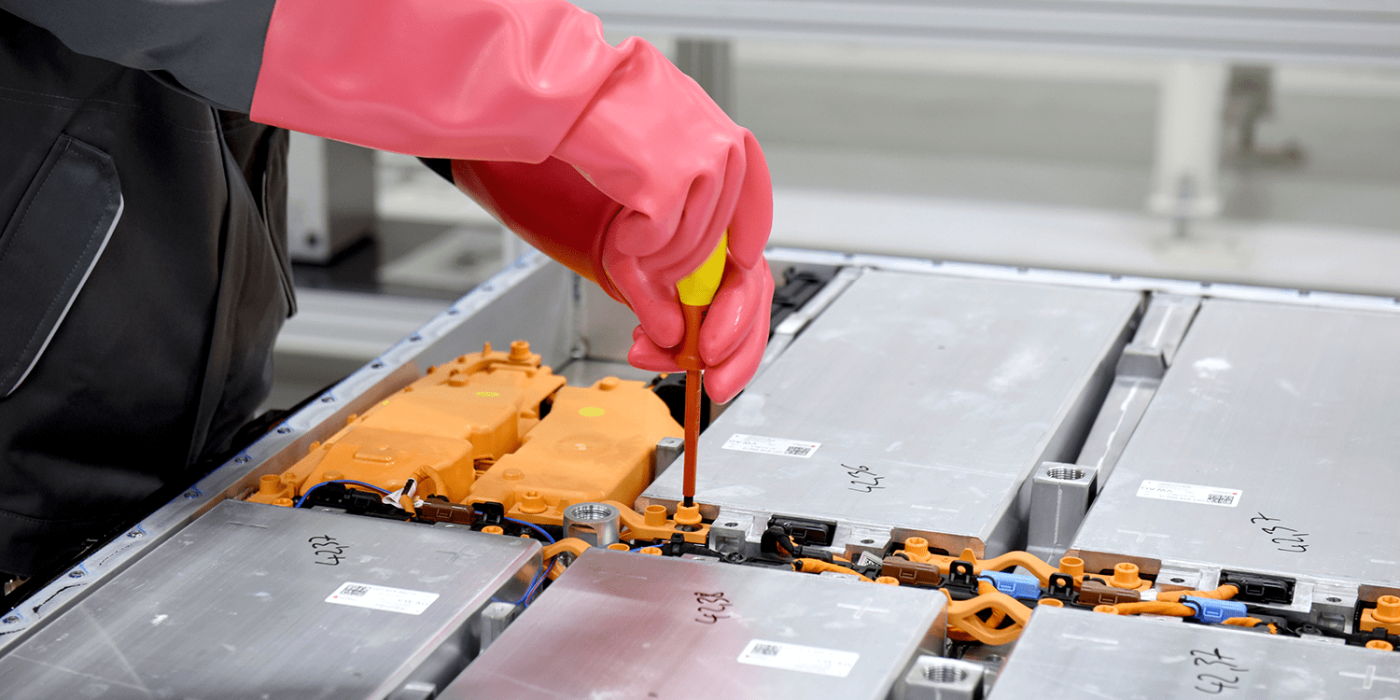
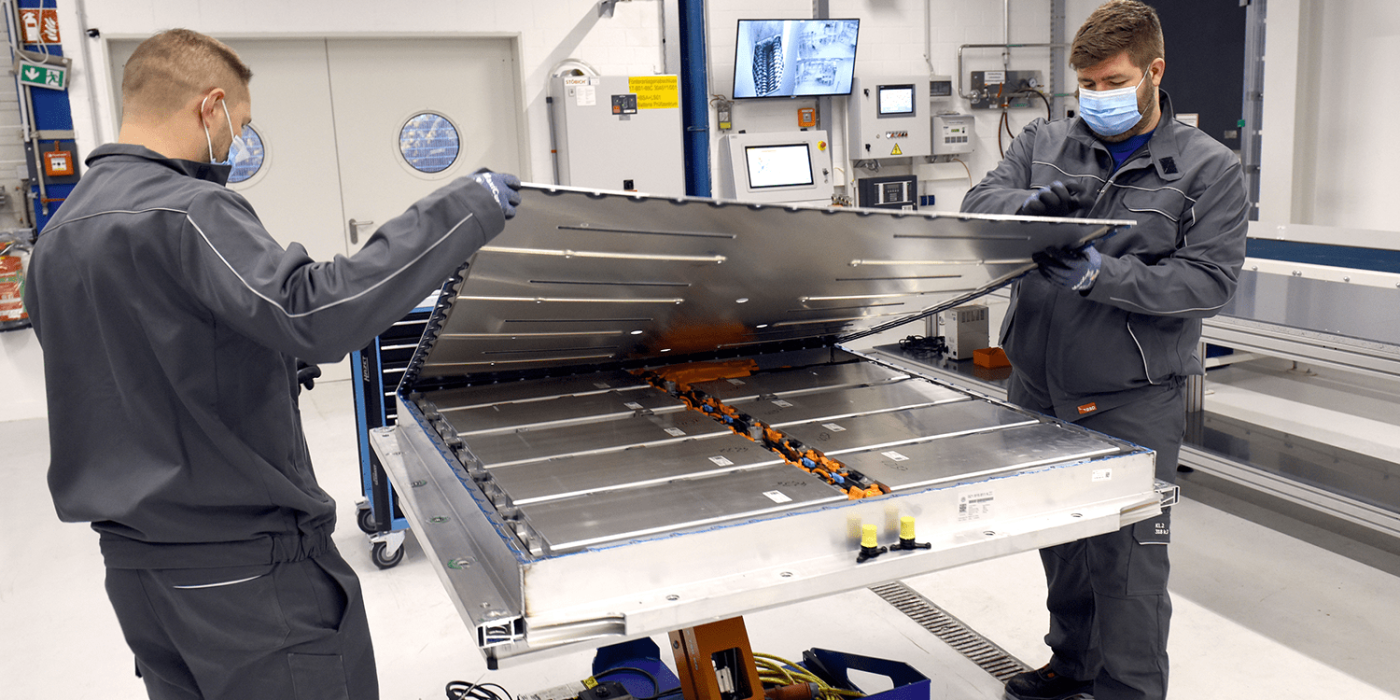
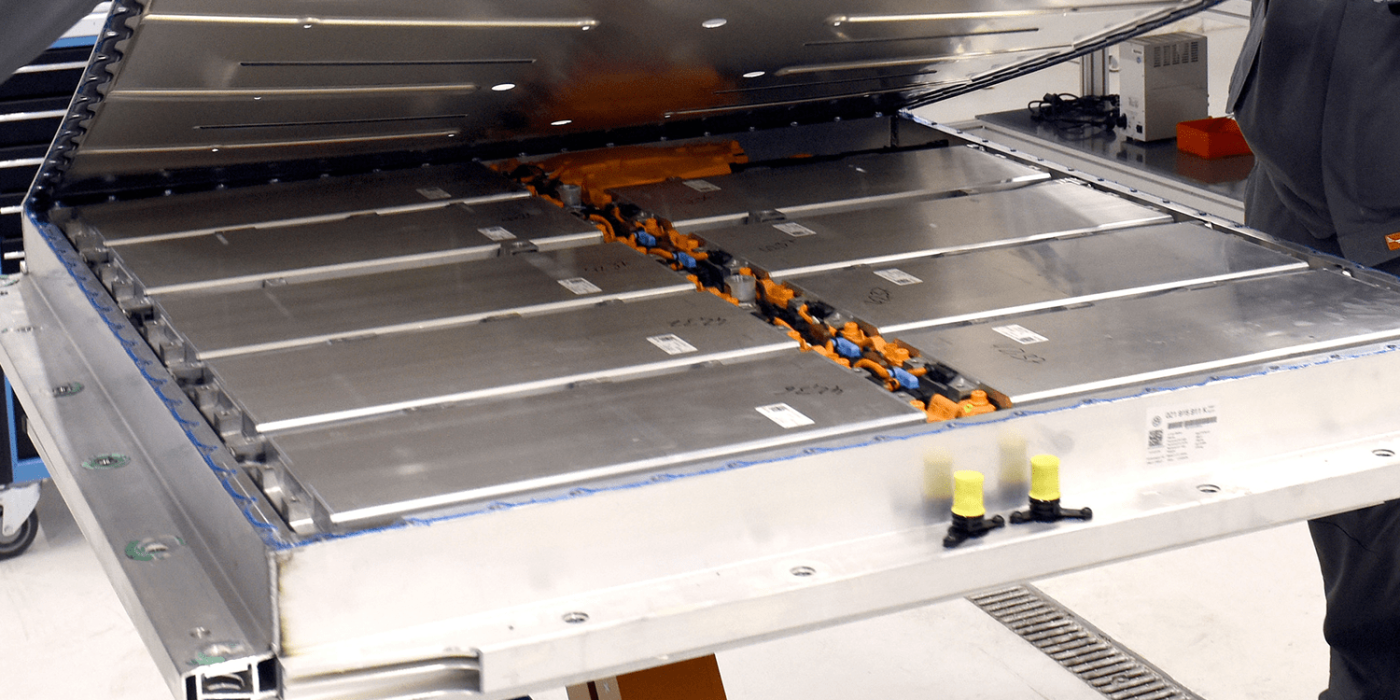
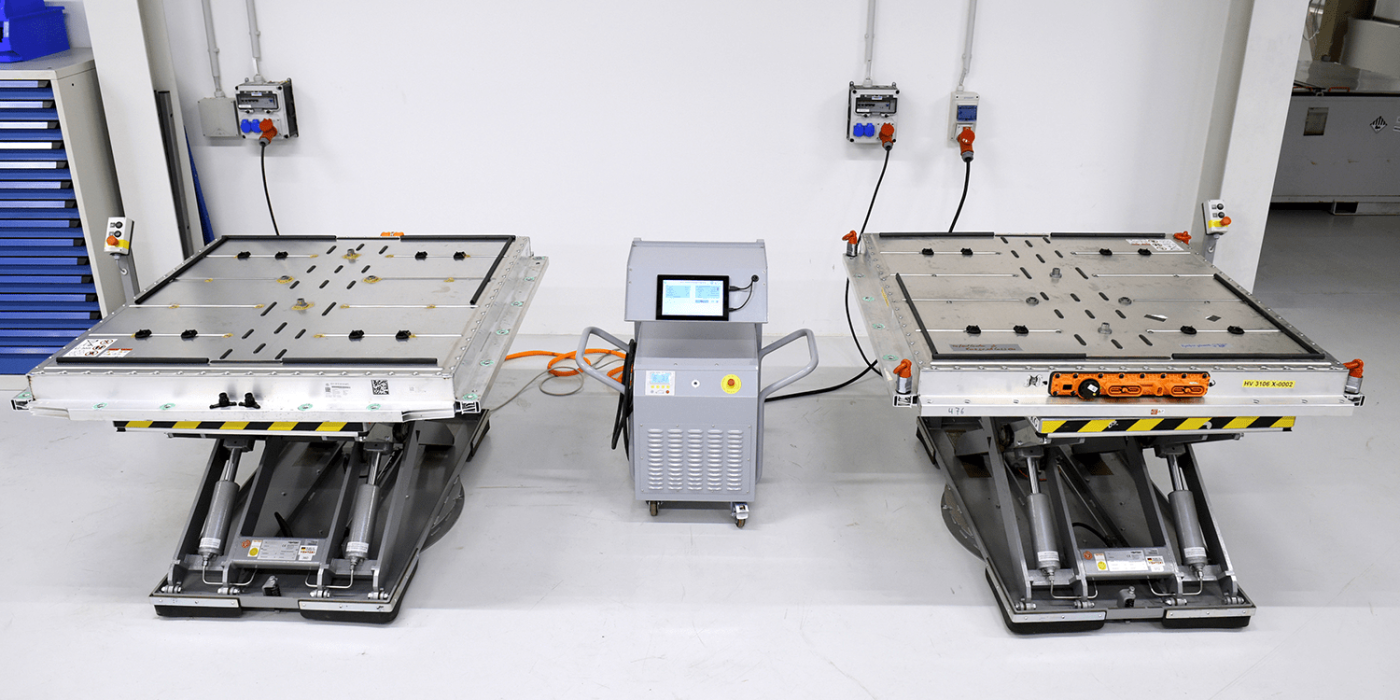

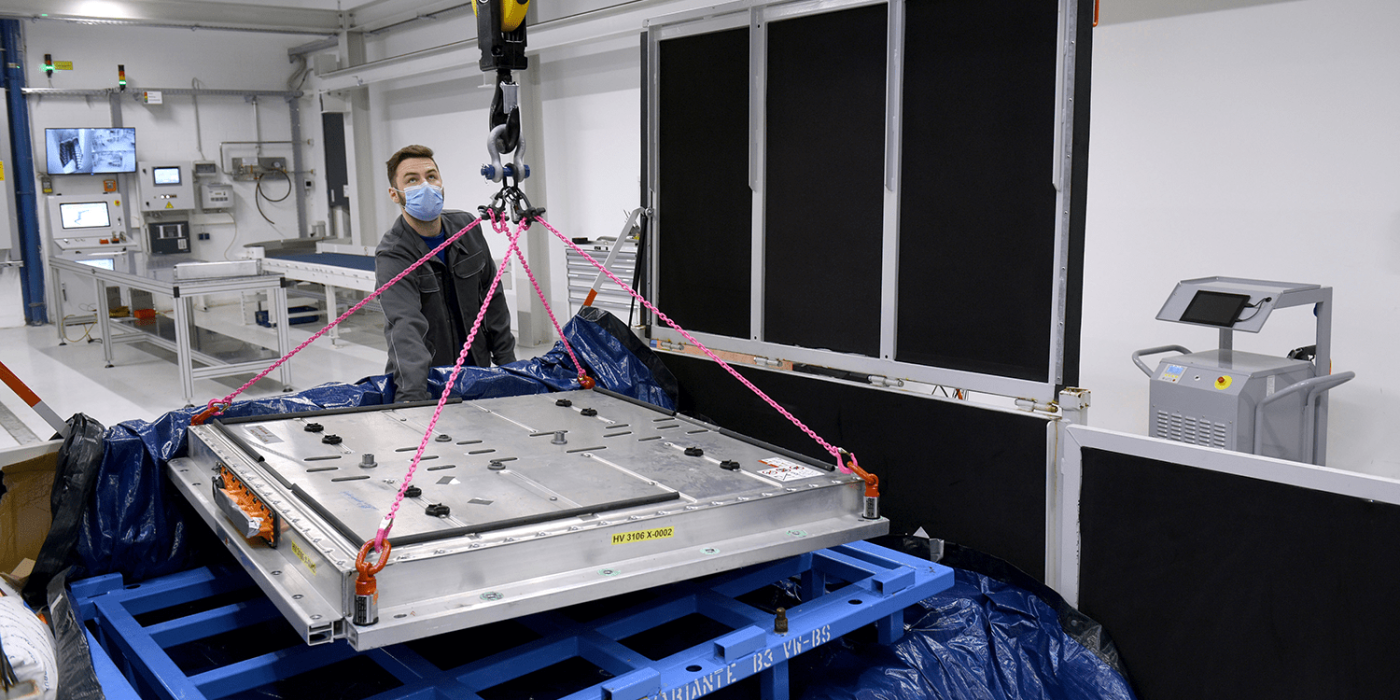
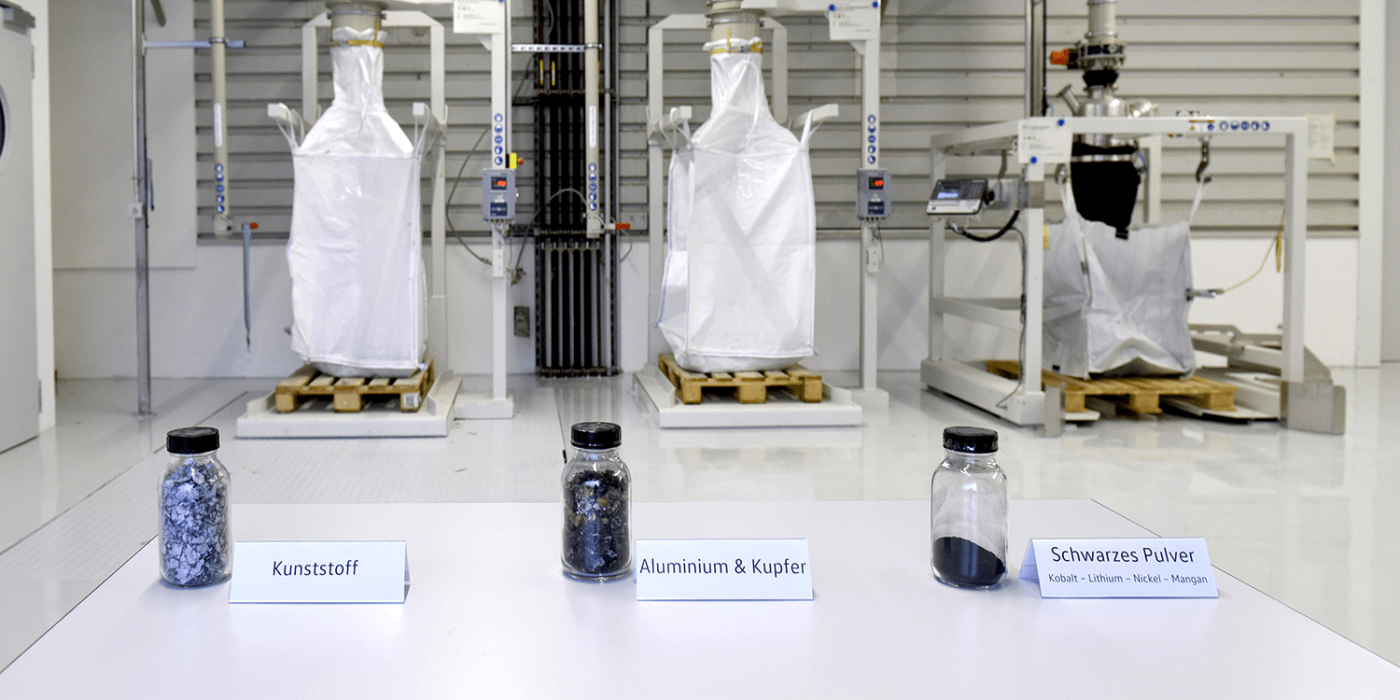
“It will only be in the medium or long term that we will start to feed the materials back into the manufacturing of new products,” said Thomas Schmall, member of the Group Executive Board and head of VWGC, at an online event to mark the opening of the pilot plant. “Still, it’s important that we get into these issues early. If we hadn’t invested in the production of electric machines in Kassel ten years ago, we wouldn’t be able to build electric motors for the MEB today to this extent and quality.”
The batteries to be recycled at the start of the plant will cost around six million euros and come from the group. “We have been talking to all the Group brands for a year and a half and have collected and stored the batteries from their test and pre-production vehicles,” Schmall said. “We are also recycling prototype cells from our pilot cell production in Salzgitter. This will enable us to utilise the plant well this year.”
VWGC does not cover all the steps at the Salzgitter site itself; partner companies carry out some processes. After the incoming inspection for second-life use, the batteries are deep-discharged and dismantled. The individual parts are then ground into granulate and melted down in a non-energy-intensive process. Aluminium, copper, plastics and the “black powder” can then be recovered from the dried granulate (to recover the electrolyte). This powder contains, among other things, the lithium, nickel, manganese and cobalt as well as graphite.
The “black powder” is then processed by “specialised partners” in a so-called hydrometallurgical process – i.e. with the use of water and chemicals – to prepare the individual raw materials.
Nine kilos of cobalt, eight kilos of lithium
With the previous pyrometallic processes, which melted down the battery materials, only about 50 per cent of the materials could be recovered so far – the focus here was on nickel and cobalt.
The list of materials that can be recovered in the hydrometallurgical process is much longer. During the presentation, VW also mentions the individual quantities of the materials used. The 62-kWh battery of the MEB (total weight 400 kilograms) contains around 126 kilograms of aluminium (mainly in the housing), 71 kilograms of graphite and 22 kilograms of copper. Wolfsburg gives the weights of the crucial cathode materials used as 12 kilogrammes of manganese, 9 kilogrammes of cobalt and 8 kilogrammes of lithium.
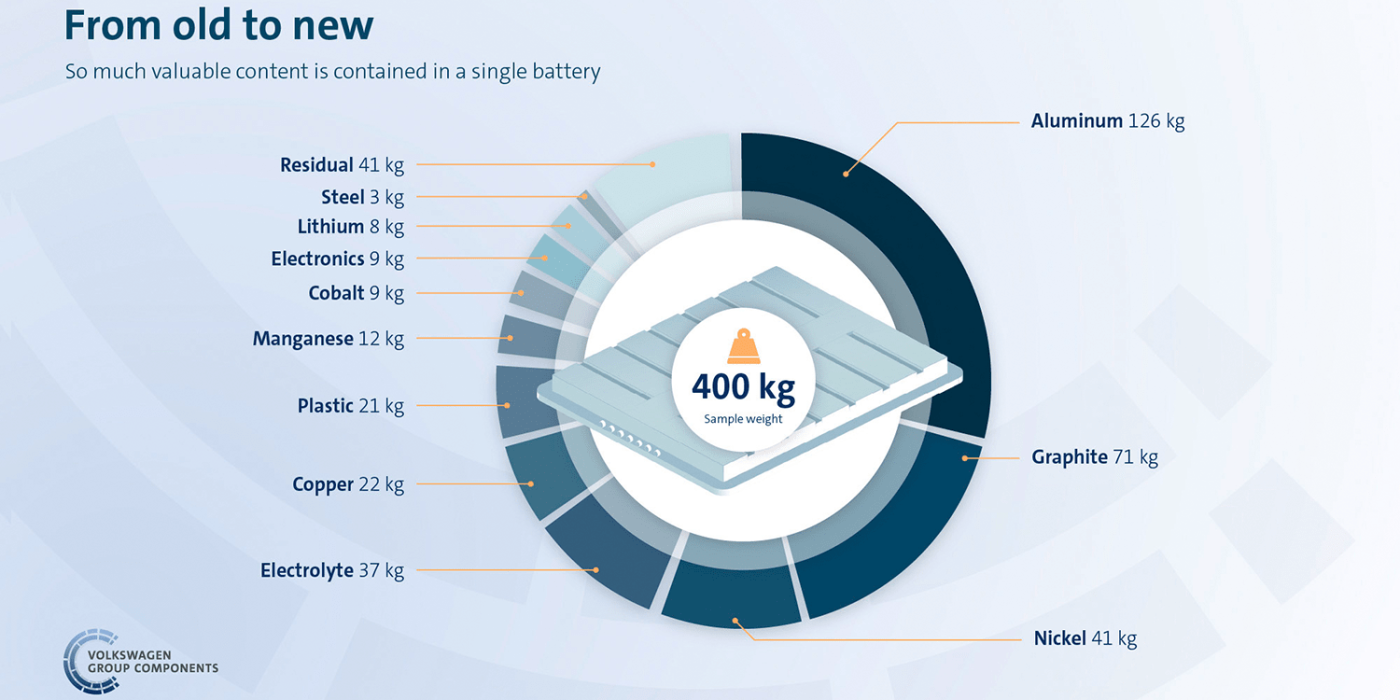
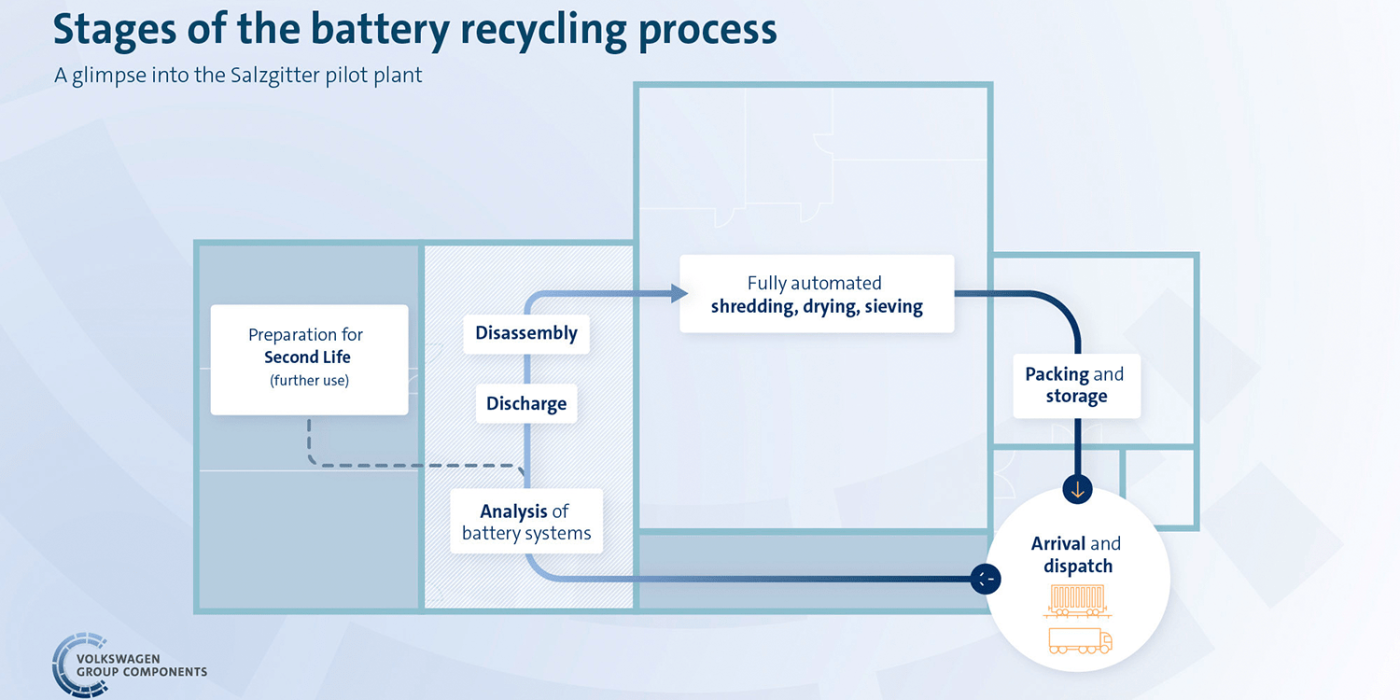
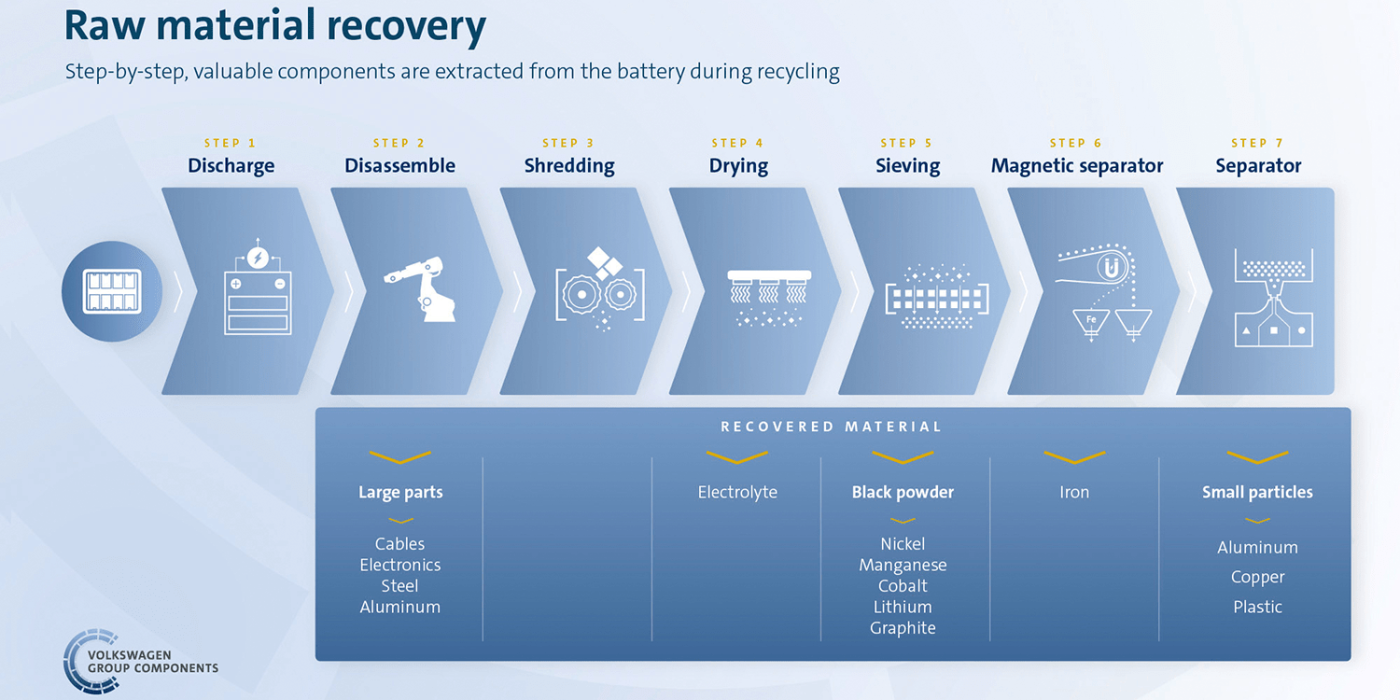
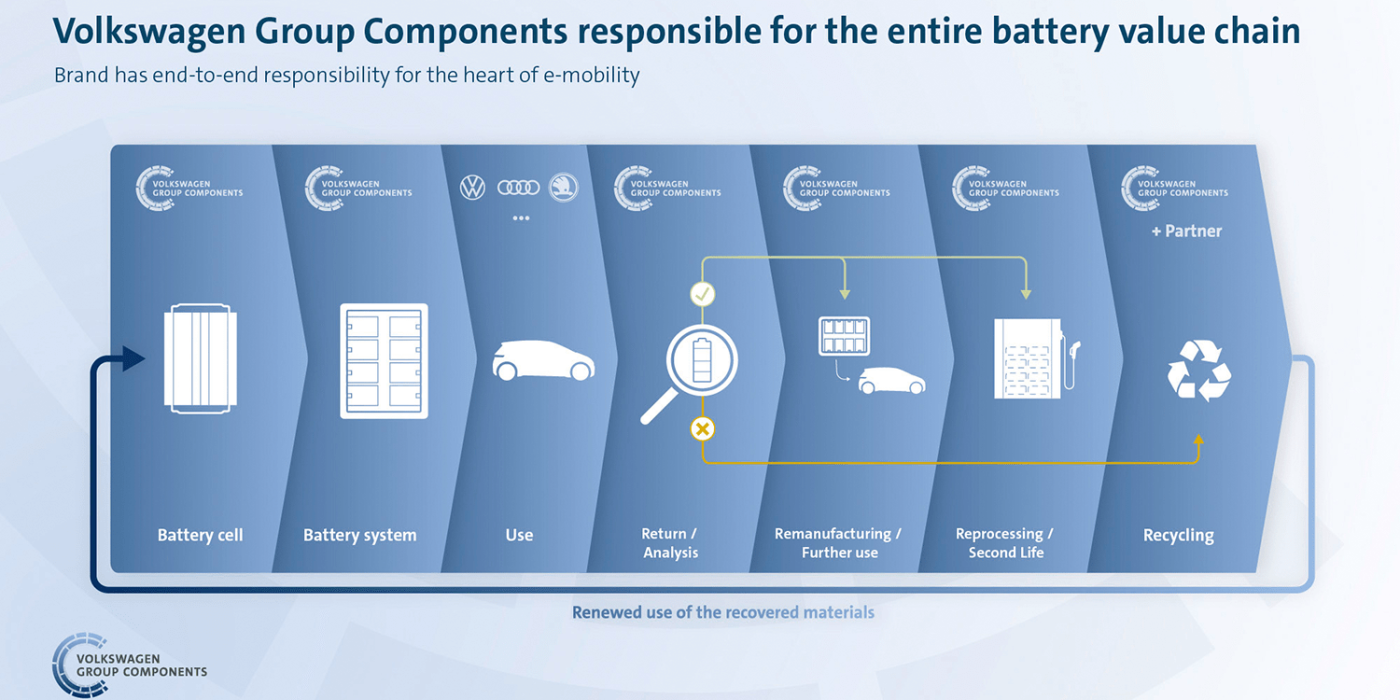
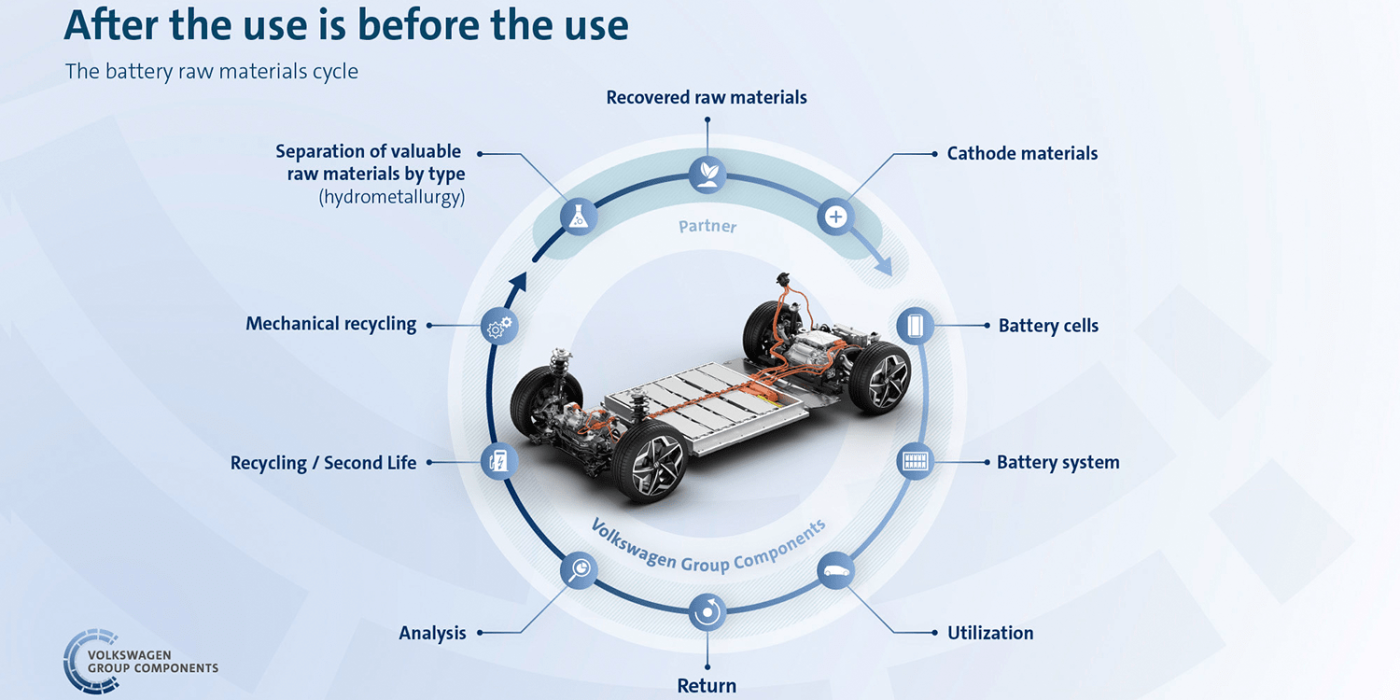
“As a consequence, essential components of old battery cells can be used to produce new cathode material,” says Mark Möller, Head of Business Unit Technical Development & E-Mobility. “From research, we know that recycled battery raw materials are just as efficient as new ones. In future, we intend to support our battery cell production with the material we recover. Given that the demand for batteries and the related raw materials will increase drastically, we can put every gram of recycled material to good use.”
1.3 tonnes less CO2 with recycled material
But not all materials can yet be used directly in new batteries. The recovered graphite is not of the quality needed for new batteries, VW says. And components like the dried electrolyte cannot be reused as an electrolyte, but for other chemical industry uses.
For a 62 kWh battery (marketed in the ID.3 with its net 58 kWh), Volkswagen Group Components puts the CO2 saving at around 1.3 tonnes if the cathodes are made from recycled material and with green electricity.
In addition to its plant, the company is also looking into cooperation with other recycling companies, Möller said. “We don’t intend to recycle every single battery in the world ourselves. But partners must follow similar processes as we do.”
With reporting by Sebastian Schaal, Germany.
0 Comments